Method for optimizing workpiece clamping positions during milling machining by robot
A milling processing and workpiece clamping technology, applied in the field of robot milling process optimization, can solve the problems of reduced tool life, reduced workpiece surface quality, reduced system reliability, etc., to reduce the degree of chatter, reduce the risk of chatter, ensure The effect of quality and dimensional accuracy
- Summary
- Abstract
- Description
- Claims
- Application Information
AI Technical Summary
Problems solved by technology
Method used
Image
Examples
Embodiment Construction
[0036] Embodiments of the present invention will be described in detail below in conjunction with the accompanying drawings.
[0037] Such as figure 1 As shown, the robot milling chatter analysis platform is composed of a robot 1, an electric spindle 2, an acceleration sensor 3, a force hammer 4, a vibration acquisition instrument 5, a computer 6, a workpiece to be processed 7, a fixture 8, and a workbench 9. The electric spindle 2 is installed on the end effector of the robot 1, the acceleration sensor 3 is installed at the end of the electric spindle 2, and the acceleration sensor 3, the force hammer 4 and the computer 6 are respectively connected with the vibration collector 5.
[0038] Such as figure 2 As shown, a method for optimal planning of the workpiece clamping position in robot milling, based on the chatter stability domain analysis method, includes the following steps:
[0039] The first step: if image 3 As shown, when the relative positions of the workbench 9...
PUM
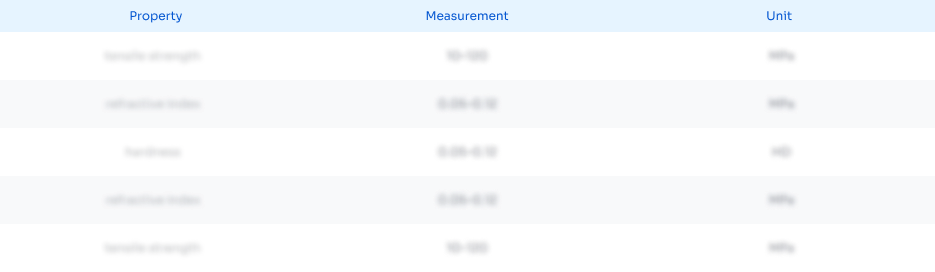
Abstract
Description
Claims
Application Information

- R&D
- Intellectual Property
- Life Sciences
- Materials
- Tech Scout
- Unparalleled Data Quality
- Higher Quality Content
- 60% Fewer Hallucinations
Browse by: Latest US Patents, China's latest patents, Technical Efficacy Thesaurus, Application Domain, Technology Topic, Popular Technical Reports.
© 2025 PatSnap. All rights reserved.Legal|Privacy policy|Modern Slavery Act Transparency Statement|Sitemap|About US| Contact US: help@patsnap.com