A kind of preparation method of zirconium compound doped high-temperature corrosion-resistant nickel-based alloy
A nickel-based alloy, corrosion-resistant technology, applied in the field of alloys, can solve the problems of alloy performance and corrosion resistance reduction, hardenability, fracture toughness, corrosion and other problems, to improve service performance and life, excellent durability Alkali corrosion performance, the effect of simple process
- Summary
- Abstract
- Description
- Claims
- Application Information
AI Technical Summary
Problems solved by technology
Method used
Examples
Embodiment 1
[0021] 1. Raw material preparation: take the raw material according to the weight ratio of nickel: chromium: zirconia: vanadium oxide: carbon=64.5: 33.5: 1.2: 0.59: 1.6, wherein the purity of metallic nickel is more than or equal to 99.9%, the purity of metallic chromium is more than or equal to 99.9%, The purity of zirconia ≥ 99.8%, the purity of vanadium ≥ 99.8%, and the purity of carbon ≥ 99%. Zirconia, vanadium oxide and carbon are preferably granular or powdery, and zirconia, vanadium oxide and carbon are mixed and pressed into pellets (balls The diameter is 0-30mm, and the pressure ball makes the contact sufficient to make the thermal reduction reaction more efficient).
[0022] 2. Melting: Put nickel and chromium into the vacuum induction furnace for smelting, control the melting temperature of the vacuum induction furnace to 1650°C, after the nickel and chromium are melted, then mix and press the pellets made of zirconia, vanadium oxide and carbon Throw it into a vacuu...
Embodiment 2
[0028] 1. Raw material preparation: take the raw material according to the weight ratio of nickel: chromium: zirconia: vanadium oxide: carbon=66.75: 30.3: 0.993: 0.845: 1.55, wherein, the purity of metallic nickel is more than or equal to 99.9%, the purity of metallic chromium is more than or equal to 99.9%, The purity of zirconia ≥ 99.8%, the purity of vanadium ≥ 99.8%, and the purity of carbon ≥ 99%. The zirconia, vanadium oxide and carbon are preferably granular or powdery, and the zirconia, vanadium oxide and carbon are mixed and pressed into pellets.
[0029] 2. Melting: Put nickel and chromium into the vacuum induction furnace for smelting, control the melting temperature of the vacuum induction furnace to 1600°C, after the nickel and chromium are melted, then mix and press the pellets made of zirconia, vanadium oxide and carbon Throw it into a vacuum induction furnace for smelting, control the smelting time after the pellets are put into the vacuum induction furnace to b...
Embodiment 3
[0035] 1. Raw material preparation: take the raw material according to the weight ratio of nickel: chromium: zirconia: vanadium oxide: carbon=63.5: 27.5: 0.85: 0.55: 1.15, wherein, the purity of metallic nickel is more than or equal to 99.9%, the purity of metallic chromium is more than or equal to 99.9%, The purity of zirconia ≥ 99.8%, the purity of vanadium ≥ 99.8%, and the purity of carbon ≥ 99%. The zirconia, vanadium oxide and carbon are preferably granular or powdery, and the zirconia, vanadium oxide and carbon are mixed and pressed into pellets.
[0036] 2. Melting: Put nickel and chromium into the vacuum induction furnace for smelting, and control the melting temperature of the vacuum induction furnace to 1550°C. After the nickel and chromium are melted, the balls made of zirconia, vanadium oxide and carbon are mixed and pressed. Throw it into a vacuum induction furnace for smelting, control the smelting time after the pellets are put into the vacuum induction furnace t...
PUM
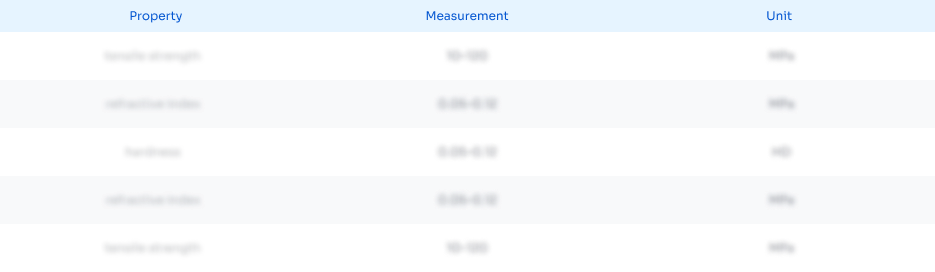
Abstract
Description
Claims
Application Information

- Generate Ideas
- Intellectual Property
- Life Sciences
- Materials
- Tech Scout
- Unparalleled Data Quality
- Higher Quality Content
- 60% Fewer Hallucinations
Browse by: Latest US Patents, China's latest patents, Technical Efficacy Thesaurus, Application Domain, Technology Topic, Popular Technical Reports.
© 2025 PatSnap. All rights reserved.Legal|Privacy policy|Modern Slavery Act Transparency Statement|Sitemap|About US| Contact US: help@patsnap.com