Method for preparing boron nitride ceramic material through stepped sintering
A ceramic material and step-by-step sintering technology, which is applied in the field of step-by-step sintering to prepare boron nitride ceramic materials, can solve the problems of difficult discharge of impurities such as gases, affect the density and strength of ceramic materials, and complex processes, and achieve the goal of increasing density and strength. Effect
- Summary
- Abstract
- Description
- Claims
- Application Information
AI Technical Summary
Problems solved by technology
Method used
Examples
Embodiment 1
[0021] Prepare boron nitride-based powder, wherein the additive is SiC, the content is 20wt.%, the sintering aid is B2O3, the content is 8wt.%, boron nitride is the balance, and several powders are mixed evenly.
[0022] The mixed powders are put into graphite molds for hot pressing and sintering.
[0023] In the hot pressing sintering step, the low temperature holding step is 600°C, and the holding time is 1.5 hours; the medium temperature holding step is 1300°C, the pressure is 18MPa, and the holding time is 2 hours; the high temperature holding step is 1800°C, the pressure is 20MPa, and the holding time The time is 2 hours.
[0024] The material after sintering is taken out to obtain boron nitride ceramic material.
Embodiment 2
[0026] Prepare boron nitride-based powder, wherein the additive is Si4N3, the content is 20wt.%, the sintering aid is B2O3, the content is 8wt.%, boron nitride is the balance, and several powders are mixed evenly.
[0027] The mixed powders are put into graphite molds for hot pressing and sintering.
[0028] In the hot pressing sintering step, the low temperature holding step is 800°C, and the holding time is 1.5 hours; the medium temperature holding step is 1200°C, the pressure is 20MPa, and the holding time is 2 hours; the high temperature holding step is 1900°C, the pressure is 18MPa, and the holding time The time is 1.5 hours.
[0029] The material after sintering is taken out to obtain boron nitride ceramic material.
Embodiment 3
[0031] Prepare boron nitride-based powder, in which the additive is CaO, the content is 18wt.%, the sintering aid is B2O3, the content is 8wt.%, boron nitride is the balance, and several powders are mixed evenly.
[0032] The mixed powders are put into graphite molds for hot pressing and sintering.
[0033] In the hot pressing sintering step, the low temperature holding step is 700°C, and the holding time is 1.5 hours; the medium temperature holding step is 1500°C, the pressure is 18MPa, and the holding time is 2 hours; the high temperature holding step is 1900°C, the pressure is 20MPa, and the holding time The time is 1.2 hours.
[0034] The material after sintering is taken out to obtain boron nitride ceramic material.
PUM
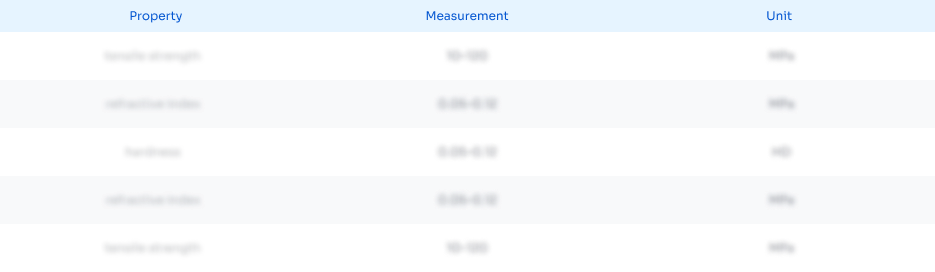
Abstract
Description
Claims
Application Information

- R&D Engineer
- R&D Manager
- IP Professional
- Industry Leading Data Capabilities
- Powerful AI technology
- Patent DNA Extraction
Browse by: Latest US Patents, China's latest patents, Technical Efficacy Thesaurus, Application Domain, Technology Topic, Popular Technical Reports.
© 2024 PatSnap. All rights reserved.Legal|Privacy policy|Modern Slavery Act Transparency Statement|Sitemap|About US| Contact US: help@patsnap.com