Auxiliary ultrasound milling technological method for laser micro-texture prefabricating and machining system
A milling and micro-texturing technology, applied in the direction of manufacturing tools, other manufacturing equipment/tools, etc., can solve the problem that the processing efficiency is difficult to greatly improve, the applicable depth of cut and feed speed are small, the wear resistance and toughness of the tool are limited, etc. problems, to achieve the effect of improving the material removal rate, diversifying the structure configuration, and reducing the tool wear
- Summary
- Abstract
- Description
- Claims
- Application Information
AI Technical Summary
Problems solved by technology
Method used
Image
Examples
Embodiment 1
[0039] see figure 1 , the laser prefabricated micro-texture-assisted ultrasonic milling processing system provided by the present invention includes a multi-axis linkage laser processing system 1 and a multi-axis linkage ultrasonic-assisted milling processing system 2, wherein the multi-axis linkage laser processing system 1 is used for the material to be processed Laser pretreatment is performed to form a prefabricated micro-texture on the material to be processed, and the multi-axis linkage ultrasonic-assisted milling system 2 is used to mill the material to be processed after laser pretreatment to form the desired product. The prefabricated micro-textures include vertical micro-groove arrays, chute arrays with a certain angle to the feed direction, grid arrays, circular hole arrays, curved groove arrays, and horizontal micro-groove arrays (see Figure 5A-5F for details).
[0040] The multi-axis linkage laser processing system 1 includes a first motion control unit 11, three ...
Embodiment 2
[0053] The functional structure of the laser prefabricated microtexture assisted ultrasonic milling processing system in this embodiment is basically the same as that of the laser prefabricated microtexture assisted ultrasonic milling processing system in Embodiment 1. The difference is that the multi-axis linkage laser processing system 1 and the multi-axis linkage ultrasonic-assisted milling processing system 2 in this embodiment are integrated online to realize dynamic synchronous large-scale matching processing, and the degree of freedom of rotation of the material to be processed relative to the ultrasonic tool is determined by The swing of the ultrasonic-assisted milling table 24 of the multi-axis linkage ultrasonic-assisted milling processing system 2 is realized, and the spatial attitude of the material to be processed after laser pretreatment relative to the laser beam is realized by the swing of the laser beam.
[0054] In the working state, the laser beam of the mult...
Embodiment 3
[0057] The functional structure of the laser prefabricated microtexture assisted ultrasonic milling processing system in this embodiment is basically the same as that of the laser prefabricated microtexture assisted ultrasonic milling processing system in Embodiment 2. The difference is that the degree of freedom of rotation of the material to be processed relative to the ultrasonic tool after laser pretreatment is realized by the swing of the spindle 25 of the multi-axis linkage ultrasonic-assisted milling system 2, and the spatial attitude of the material to be processed relative to the laser beam is determined by the laser beam swing implementation.
[0058] Compared with the structure shown in Embodiment 2, this structure is more suitable for processing large-scale structural workpieces.
PUM
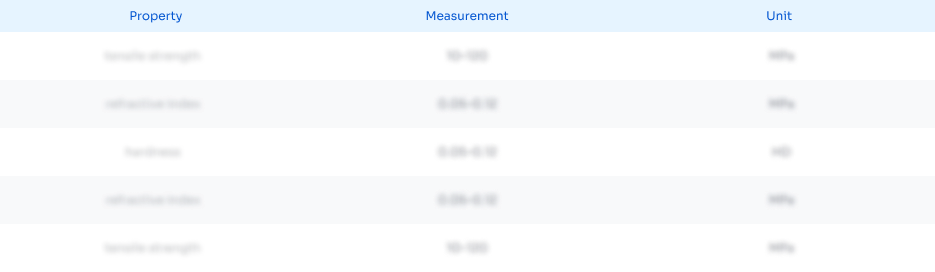
Abstract
Description
Claims
Application Information

- Generate Ideas
- Intellectual Property
- Life Sciences
- Materials
- Tech Scout
- Unparalleled Data Quality
- Higher Quality Content
- 60% Fewer Hallucinations
Browse by: Latest US Patents, China's latest patents, Technical Efficacy Thesaurus, Application Domain, Technology Topic, Popular Technical Reports.
© 2025 PatSnap. All rights reserved.Legal|Privacy policy|Modern Slavery Act Transparency Statement|Sitemap|About US| Contact US: help@patsnap.com