Integrated welding device for microwave component
A microwave component and welding device technology, applied in auxiliary devices, welding equipment, auxiliary welding equipment, etc., can solve the problems of poor welding quality consistency, low welding efficiency, affecting welding quality, etc., and achieve good welding quality consistency and welding positioning. High precision, convenient and quick installation
- Summary
- Abstract
- Description
- Claims
- Application Information
AI Technical Summary
Problems solved by technology
Method used
Image
Examples
Embodiment Construction
[0041] In order to make the object, technical solution and advantages of the present invention clearer, various embodiments of the present invention will be described in detail below in conjunction with the accompanying drawings.
[0042] Please refer to the following Figure 1 to Figure 12 , an integrated welding device for microwave components 5, used for welding microwave components 5 including a box body 51, a microwave substrate 57, a glass bead 52 and a connector 54, which includes a base 1, an upper pressing module 2, a left Press die group 3 and right press die group 4; Wherein,
[0043]The left pressing module 3 includes a left pressing block 31, a self-locking buckle 6 and a pogo pin 9, the right pressing module 4 includes a right pressing block 41, a self-locking buckle 6 and a pogo pin 9, and the upper pressing module 2 includes an upper pressing Block 23, self-locking buckle 6 and pogo pin 9, left pressing block 31, right pressing block 41 and upper pressing bloc...
PUM
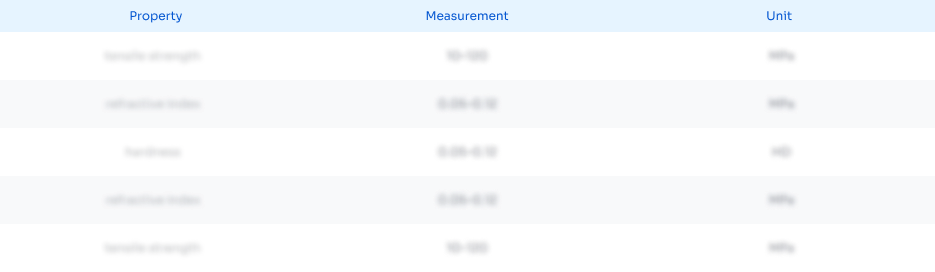
Abstract
Description
Claims
Application Information

- R&D
- Intellectual Property
- Life Sciences
- Materials
- Tech Scout
- Unparalleled Data Quality
- Higher Quality Content
- 60% Fewer Hallucinations
Browse by: Latest US Patents, China's latest patents, Technical Efficacy Thesaurus, Application Domain, Technology Topic, Popular Technical Reports.
© 2025 PatSnap. All rights reserved.Legal|Privacy policy|Modern Slavery Act Transparency Statement|Sitemap|About US| Contact US: help@patsnap.com