Fine ferric oxide desulfurizing agent and preparation method and application method thereof
A technology of iron oxide concentrate and desulfurizer, which is applied in chemical instruments and methods, separation methods, and dispersed particle separation, can solve the problems of single desulfurization function, cumbersome operation, and poor removal effect, so as to improve H2S removal accuracy and Sulfur capacity, improving removal accuracy and removal rate, promoting hydrogenolysis or hydrolysis
- Summary
- Abstract
- Description
- Claims
- Application Information
AI Technical Summary
Problems solved by technology
Method used
Examples
preparation example Construction
[0031] The preparation method of described iron oxide fine desulfurizer, carries out successively according to the following steps:
[0032] S10: Add solid ferrous sulfate heptahydrate powder and solid calcium hydroxide powder into the kneader, mix, stir, and react at room temperature for 15-30 minutes, adding an appropriate amount of water during the stirring process. Wherein, the solid ferrous sulfate heptahydrate powder is added by the initial mass percentage, the solid calcium hydroxide powder is added by 30% to 70% of the mass percentage, and the water yield is 2% to 5% of the total weight of the material added in this step. %.
[0033] S20: After the reaction in step S10 is completed, add solid copper sulfate pentahydrate powder and solid sodium hydroxide powder into the kneader, and continue to stir, mix, and react with the materials in the kneader at room temperature for 25 to 50 minutes, and add bentonite during the stirring process , sodium carboxymethyl cellulose a...
Embodiment 1
[0039] Accurately weigh 66g of solid ferrous sulfate heptahydrate powder, 18g of solid calcium hydroxide powder, 4g of solid copper sulfate pentahydrate powder, 7g of solid sodium hydroxide powder, 3g of sodium bentonite, and 2g of sodium carboxymethylcellulose for later use.
[0040] Add 66g of solid ferrous sulfate heptahydrate powder and 10.8g of solid calcium hydroxide powder into the kneader, mix, stir and react at room temperature for 30 minutes, and add 2g of water during the stirring process. After the reaction was completed, 4g of solid copper sulfate pentahydrate powder and 7g of solid sodium hydroxide powder were added to the kneader, and the materials in the kneader were continuously stirred, mixed, and reacted for 40 minutes at room temperature. During the stirring process, 1.5g of bentonite, 1g of Sodium carboxymethylcellulose and 0.2 g of water. After the reaction was completed, 7.2g of solid calcium hydroxide powder was added to the kneader, and the material in...
Embodiment 2
[0043] Accurately weigh 68g of solid ferrous sulfate heptahydrate powder, 18g of solid calcium hydroxide powder, 3g of solid copper sulfate pentahydrate powder, 7g of solid sodium hydroxide powder, 3g of sodium bentonite, and 1g of sodium carboxymethylcellulose for later use.
[0044] Add 68g of solid ferrous sulfate heptahydrate powder and 12.6g of solid calcium hydroxide powder into the kneader, mix, stir and react at room temperature for 30 minutes, and add 3.5g of water during the stirring process. After the reaction was completed, 3g of solid copper sulfate pentahydrate powder and 7g of solid sodium hydroxide powder were added to the kneader, and the materials in the kneader were continuously stirred, mixed, and reacted for 50 minutes at room temperature. During the stirring process, 1.8g of bentonite, 0.5 g sodium carboxymethylcellulose and 0.25 g water. After the reaction was completed, 5.4g of solid calcium hydroxide powder was added to the kneader, and the material in...
PUM
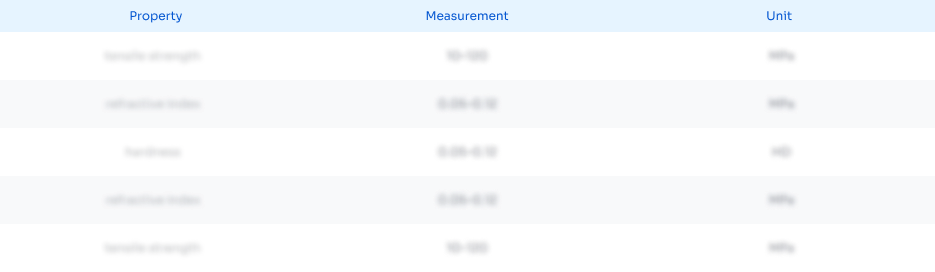
Abstract
Description
Claims
Application Information

- R&D Engineer
- R&D Manager
- IP Professional
- Industry Leading Data Capabilities
- Powerful AI technology
- Patent DNA Extraction
Browse by: Latest US Patents, China's latest patents, Technical Efficacy Thesaurus, Application Domain, Technology Topic, Popular Technical Reports.
© 2024 PatSnap. All rights reserved.Legal|Privacy policy|Modern Slavery Act Transparency Statement|Sitemap|About US| Contact US: help@patsnap.com