Wire Cutting Power Control System
A technology of power supply control and wire cutting, which is applied to circuits, manufacturing tools, electric processing equipment, etc., can solve problems such as unfavorable and stable cutting processing, power supply energy waste, and power tube temperature rise, so as to improve the cutting quality of workpieces and reduce heat. Produces the effect of constant pulse width
- Summary
- Abstract
- Description
- Claims
- Application Information
AI Technical Summary
Problems solved by technology
Method used
Image
Examples
Embodiment Construction
[0017]The following will clearly and completely describe the technical solutions in the embodiments of the present invention with reference to the accompanying drawings in the embodiments of the present invention. Obviously, the described embodiments are only some, not all, embodiments of the present invention. Based on the embodiments of the present invention, all other embodiments obtained by persons of ordinary skill in the art without making creative efforts belong to the protection scope of the present invention.
[0018] see Figure 1-4 , the present invention provides a technical solution: a wire cutting power supply control method, the control method mainly includes the following steps:
[0019] A. Set the parameters of high-frequency oscillation on the control panel of the cutting machine, and output high-frequency oscillation waves;
[0020] B. The high-frequency oscillating wave is amplified through the power amplification module in the control power supply body, a...
PUM
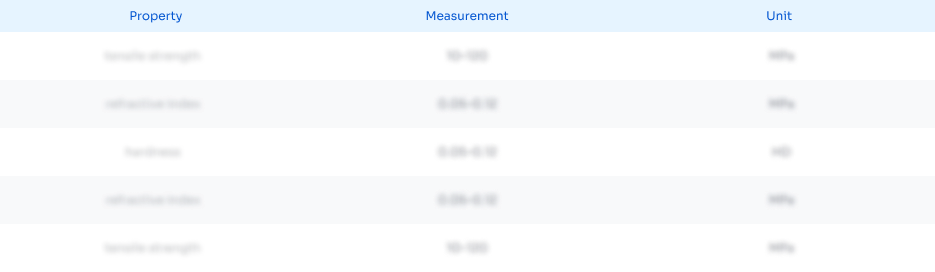
Abstract
Description
Claims
Application Information

- Generate Ideas
- Intellectual Property
- Life Sciences
- Materials
- Tech Scout
- Unparalleled Data Quality
- Higher Quality Content
- 60% Fewer Hallucinations
Browse by: Latest US Patents, China's latest patents, Technical Efficacy Thesaurus, Application Domain, Technology Topic, Popular Technical Reports.
© 2025 PatSnap. All rights reserved.Legal|Privacy policy|Modern Slavery Act Transparency Statement|Sitemap|About US| Contact US: help@patsnap.com