Swelling pressure composite forming method for large-section-difference special-shaped section pipe fitting
A compound forming and large cross-section technology, which is applied in the field of expansion-compression compound forming, can solve the problem that the pipe fittings with complex cross-section shapes and special-shaped cross-sections cannot be obtained, and achieve the effect of uniform distribution of circumferential wall thickness and low requirements
- Summary
- Abstract
- Description
- Claims
- Application Information
AI Technical Summary
Problems solved by technology
Method used
Image
Examples
specific Embodiment approach 1
[0042] Specific implementation mode one: combine Figure 1 to Figure 9 Explain that a method of expansion-compression composite forming of large cross-section pipe fittings with different cross-sections in this embodiment is carried out according to the following steps:
[0043] Step 1. Determine the perimeter and equivalent diameter of several cross-sections on the pipe fitting with large cross-section difference and complex special-shaped cross-section to be formed, so as to determine the structure of the expansion-compression composite forming die and the inner cavity size and initial position of the extrusion die; The composite forming die is mainly composed of a bulging die assembled as one and an extrusion die slidingly installed in the bulging die;
[0044] Step 2: Take a tube blank 2 with a certain length and a circular cross-section of equal diameter, put it into the expansion-compression composite forming mold, and clamp the tube blank 2 with a circular cross-section...
specific Embodiment approach 2
[0049] Specific implementation mode two: combination figure 1 , figure 2 , image 3 , Figure 4 as well as Image 6 Note that the difference between this embodiment and the first embodiment is that the expansion-compression composite forming mold in step two is heated to the forming temperature of the equal-diameter circular cross-section tube blank 2 by the heating rod 8 . In this way, the expansion-compression composite forming mold in step 2 has been heated to the forming temperature of the equal-diameter circular-section tube blank 2 before placing the equal-diameter circular-section tube blank 2, the upper mold 1-1 of the bulging mold, and the lower mold of the bulging mold 1-2. The temperature of the upper die 5-1 of the lateral extrusion die and the lower die 5-2 of the lateral extrusion die can be controlled by the heating rod 8 in the heating hole 7. Other steps are the same as in the first embodiment.
specific Embodiment approach 3
[0050] Specific implementation mode three: combination Figure 1-Figure 6 Note, the difference between this embodiment and one of the specific embodiments 1 to 2 is that the sealing left punch 41 and right punch 42 in step 2 are tapered punches or shoulder punches. The beneficial effect of this specific embodiment is: the sealing punch in step 2 can be Figure 1-Figure 4 The tapered punch shown can also be a Figure 5 with Image 6 The shouldered punch 6 is shown. When the tapered punch is used to seal the end of the tube blank, the end of the tube blank is flared and then pressed against the two sides of the mold with the punch to form a rigid seal with good sealing effect and simple operation. It is suitable for applications that do not require bulging The bulging process of zone feeding. The shouldered punch relies on the shoulder and the end of the tube blank to achieve sealing, and at the same time, it will exert an axial force on the end of the equal-diameter circula...
PUM
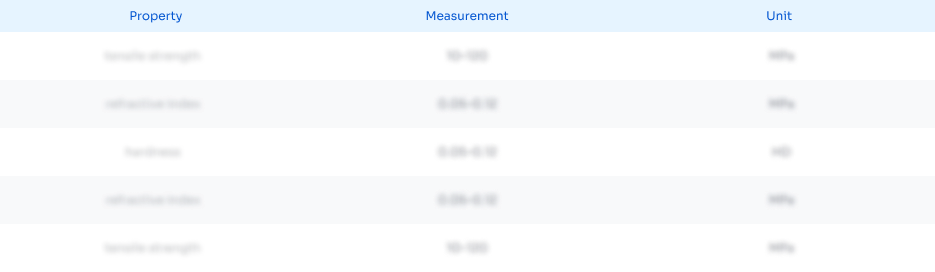
Abstract
Description
Claims
Application Information

- R&D Engineer
- R&D Manager
- IP Professional
- Industry Leading Data Capabilities
- Powerful AI technology
- Patent DNA Extraction
Browse by: Latest US Patents, China's latest patents, Technical Efficacy Thesaurus, Application Domain, Technology Topic, Popular Technical Reports.
© 2024 PatSnap. All rights reserved.Legal|Privacy policy|Modern Slavery Act Transparency Statement|Sitemap|About US| Contact US: help@patsnap.com