Medium thickness uniformization method of PCB
A medium thickness, PCB board technology, applied in the direction of electrical components, printed circuit liquid treatment, printed circuit manufacturing, etc., can solve the problems that cannot meet the requirements of impedance tolerance, difficult to achieve the production method, etc., to achieve strong operability and applicability, Avoid the effect of medium thickness difference and short process
- Summary
- Abstract
- Description
- Claims
- Application Information
AI Technical Summary
Problems solved by technology
Method used
Image
Examples
Embodiment Construction
[0030] Below, in conjunction with accompanying drawing and specific embodiment, the present invention is described further:
[0031] Such as figure 1 As shown, a method for homogenizing the medium thickness of a PCB comprises the following steps:
[0032] (1) Graphics production, making graphics on the inner copper core board;
[0033] (2) AOI inspection, AOI inspection is performed on the inner layer copper core board that has completed the graphic production;
[0034] (3) Browning treatment, browning treatment is carried out to the inner layer copper core board after AOI detection;
[0035] (4) pre-treatment of solder mask, carry out pre-treatment of solder mask to the inner layer copper core board that has completed the browning treatment;
[0036] (5) ink printing, such as figure 2 As shown, ink printing is performed on the inner copper core board that has completed the pre-soldering process by using 3D printing technology, so that the ink 8 completely fills the line ...
PUM
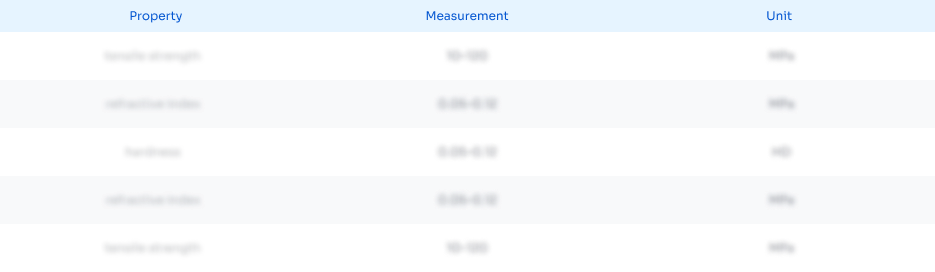
Abstract
Description
Claims
Application Information

- Generate Ideas
- Intellectual Property
- Life Sciences
- Materials
- Tech Scout
- Unparalleled Data Quality
- Higher Quality Content
- 60% Fewer Hallucinations
Browse by: Latest US Patents, China's latest patents, Technical Efficacy Thesaurus, Application Domain, Technology Topic, Popular Technical Reports.
© 2025 PatSnap. All rights reserved.Legal|Privacy policy|Modern Slavery Act Transparency Statement|Sitemap|About US| Contact US: help@patsnap.com