Fiber honeycomb composite board and preparation method thereof
A technology of honeycomb composite panels and composite panels, applied in chemical instruments and methods, synthetic resin layered products, lamination, etc., can solve problems such as low production efficiency, cumbersome operation, and increased work intensity
- Summary
- Abstract
- Description
- Claims
- Application Information
AI Technical Summary
Problems solved by technology
Method used
Image
Examples
Embodiment 1
[0037] A fiber honeycomb composite panel, the middle part of the composite panel is an aluminum honeycomb core ⑤ layer, and the two sides of the aluminum honeycomb core ⑤ layer are arranged outwards in sequence with a glass fiber ④ layer, a high-strength fiber ③ layer, a PU foam material ② layer and a mold ① layer of inner paint.
[0038] The high-strength fiber ③ layer is a carbon fiber layer. Carbon fiber has strong hiding power, high strength, low density, good coloring power, good adhesion, good wear resistance and flexibility.
[0039] The weaving method of the carbon fiber layer is twill weave, and its surface density is 200g / m 2 . According to the actual production needs of the industry to control the size of its surface density.
[0040] The surface density of glass fiber ④ is 400g / m 2 . According to the actual production needs of the industry to control the size of its surface density.
Embodiment 2
[0042] A fiber honeycomb composite panel, the middle part of the composite panel is an aluminum honeycomb core ⑤ layer, and the two sides of the aluminum honeycomb core ⑤ layer are arranged outwards in sequence with a glass fiber ④ layer, a high-strength fiber ③ layer, a PU foam material ② layer and a mold ① layer of inner paint.
[0043] The high-strength fiber layer ③ is an aramid fiber layer. Aramid fiber has excellent properties of ultra-high strength, high modulus, high temperature resistance, acid and alkali resistance, light weight, insulation, anti-aging, and long life cycle.
[0044] The weaving method of the aramid fiber layer is twill weave, and its surface density is 200g / m 2 . According to the actual production needs of the industry to control the size of its surface density.
[0045] The surface density of glass fiber ④ is 400g / m 2 . According to the actual production needs of the industry to control the size of its surface density.
Embodiment 3
[0047] A preparation method of the fiber honeycomb composite panel in embodiment 1, the steps are as follows:
[0048] 1) After diluting the mold cavity paint and MEK solvent in a ratio of 1:5 to a viscosity of 10s, spray it on the mold cavity;
[0049] 2) Lay each layer in sequence according to the carbon fiber layer, glass fiber layer ④, aluminum honeycomb core ⑤ layer, glass fiber ④ layer, and carbon fiber layer;
[0050] 3) Spray PU foam material on the paved layered structure ②.
[0051] 4) Put the sprayed structure into the inner cavity of the painted mold, apply pressure, and form the composite board.
[0052] Before the step 1), spray a release agent into the mold, wipe it clean with a cotton cloth, and then control the temperature of the mold at 120°C.
PUM
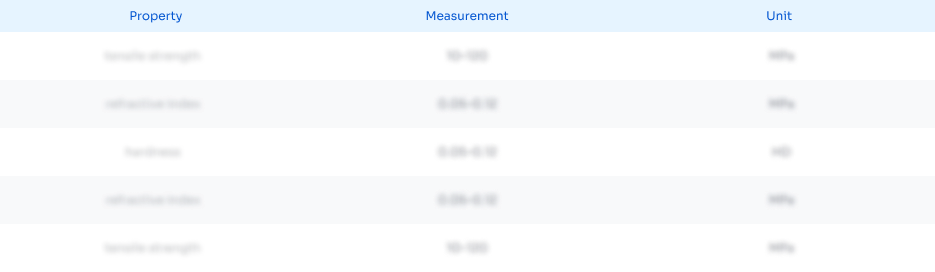
Abstract
Description
Claims
Application Information

- R&D Engineer
- R&D Manager
- IP Professional
- Industry Leading Data Capabilities
- Powerful AI technology
- Patent DNA Extraction
Browse by: Latest US Patents, China's latest patents, Technical Efficacy Thesaurus, Application Domain, Technology Topic, Popular Technical Reports.
© 2024 PatSnap. All rights reserved.Legal|Privacy policy|Modern Slavery Act Transparency Statement|Sitemap|About US| Contact US: help@patsnap.com