Multifunctional electro-hydraulic robot
A hydraulic robot, multi-functional technology, applied in the direction of manipulators, program control manipulators, claw arms, etc., to achieve advanced functions, reduce costs, save human resources and labor costs
- Summary
- Abstract
- Description
- Claims
- Application Information
AI Technical Summary
Problems solved by technology
Method used
Image
Examples
Embodiment 1
[0046] Embodiment 1, see Picture 1-1 , in this case Picture 1-1 It is a structural schematic diagram of the girder counterweight vehicle bridge 1. There are A and B pile heads connected and positioned with the outer mast 1-1 on both sides of the H beam, and there is a leg on both sides of the girder counterweight vehicle bridge 1. Telescopic hole C, installation of telescopic legs 1-4, the front end of the beam balance weight axle 1 is provided with grooves 1-6 and elliptical grooves 1-7 for installing the front drive wheel shaft and steering hydraulic cylinder, the beam balance weight The rear half of the vehicle axle 1 has four screw holes D connecting the trough type balance weight frame 1-3, and the rear end of the crossbeam balance weight vehicle axle 1 has a bearing groove 1-5 for installing the driving wheel shaft and the bearing seat.
Embodiment 2
[0047] Embodiment 2, Figure 1-2 It is the combined structure diagram of the girder counterweight axle lifting frame
[0048] There are earrings 1-3-3 connected with the outer mast on the trough-shaped counterweight frame 1-3, and there are four screw holes at the bottom of the trough-shaped counterweight frame 1-3 and the screw holes D of the girder counterweight axle 1 In this way, a double balance weight protection with a low center of gravity is formed, which ensures that the telescopic mechanical arm will not roll over when the hand rotates left and right. The inner mast lifting hydraulic cylinder 1-2-1 is installed in the groove In the groove before the type counterweight frame 1-3, the inner mast lifting hydraulic cylinder 1-2-1 is connected with the top beam of the inner mast, and the lower connecting beam 1-2-2 of the inner mast The lifting hydraulic cylinder 1-2-3 of the beam bracket lifting trolley is installed on it, and the telescopic outrigger 1-4 is connected w...
Embodiment 3
[0049] Embodiment 3, diagram 2-1 , Figure 2-2 It is the combination structure diagram of the control platform 2 of the suspension cantilever bracket lifting trolley
[0050] The lifting slide 2-1 is connected with the double H-shaped cantilever bracket 2-1-2, the bearing seat 2-1-3, the hydraulic rack cylinder 2-1-4, and the pinion 2-1-5. The storage battery 2-2 and the hydraulic package 2-2-1 are installed at the tail of the control platform to ensure the balance and stability of the control platform 2-3 and the multi-section telescopic boom. The instrument panel integrates the electric control system 2-3-2 and Steering wheel 2-3-1 is installed on the front end of described control platform 2-3, helps operator to operate conveniently.
PUM
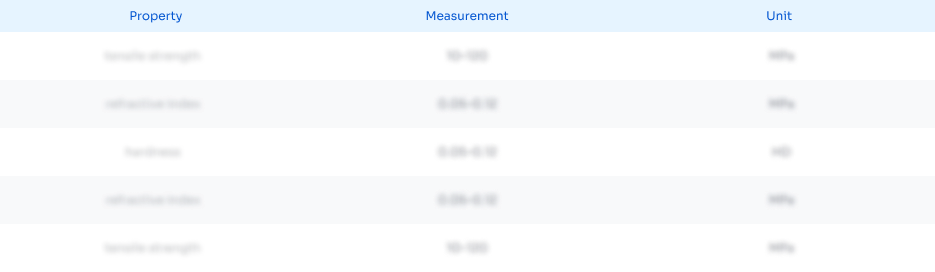
Abstract
Description
Claims
Application Information

- Generate Ideas
- Intellectual Property
- Life Sciences
- Materials
- Tech Scout
- Unparalleled Data Quality
- Higher Quality Content
- 60% Fewer Hallucinations
Browse by: Latest US Patents, China's latest patents, Technical Efficacy Thesaurus, Application Domain, Technology Topic, Popular Technical Reports.
© 2025 PatSnap. All rights reserved.Legal|Privacy policy|Modern Slavery Act Transparency Statement|Sitemap|About US| Contact US: help@patsnap.com