Preparation method of propylene catalytic cracking catalyst with yield increased
A catalytic cracking and catalyst technology, applied in catalytic cracking, carbon compound catalysts, physical/chemical process catalysts, etc., can solve the problems of increasing oil slurry yield, decreasing gasoline yield, and low specific surface area, so as to increase the yield of propylene , the effect of reducing hydrogen transfer activity
- Summary
- Abstract
- Description
- Claims
- Application Information
AI Technical Summary
Problems solved by technology
Method used
Image
Examples
Embodiment 1
[0047] (1) 11.41 kg of ZSM-5 molecular sieve (silicon-aluminum ratio 25, dry basis content 92%) was mixed with 37.72 kg of deionized water, 11.53 kg of kaolin, and 11.03 kg of pseudo-boehmite, and stirred for 3 hours.
[0048] (2) Add 1.18 kg of 35 wt% hydrochloric acid to the slurry in (1), and stir for 45 minutes.
[0049] (3) Add 4.44 kg of water glass to the acidified solution and stir for 30 minutes until uniform.
[0050] (4) Add 0.51 kg of phosphoric acid to the slurry in (3), and stir for 25 minutes until uniform.
[0051] (5) Add 7.2 kg of alkaline silica sol to the above acidified slurry, stir for about 30 minutes until uniform, and obtain a catalyst slurry.
[0052] (6) The obtained catalyst slurry is spray-dried, washed with water and dried to obtain the catalyst SL-1.
Embodiment 2
[0054] (1) 13.33 kg of ZSM-5 molecular sieve (silicon-aluminum ratio 38, dry basis content 95%) was mixed with 33.53 kg of deionized water, 9.62 kg of kaolin, and 13.24 kg of pseudo-boehmite for 4 hours.
[0055] (2) Add 1.67 kg of 35 wt% hydrochloric acid to the slurry in (1), and stir for 50 minutes.
[0056] (3) Add 6.67 kg of water glass to the acidified solution and stir for 30 minutes until uniform.
[0057] (4) Add 0.61 kg of phosphoric acid to the slurry in (3), and stir for 20-30 minutes until uniform.
[0058] (5) Add 10.8 kg of alkaline silica sol to the above acidified slurry, stir for about 30 minutes until uniform, and obtain catalyst slurry.
[0059] (6) The obtained catalyst slurry is spray-dried, washed with water and dried to obtain the catalyst SL-2.
Embodiment 3
[0061] (1) 13.33 kg of ZSM-5 molecular sieve (silicon-aluminum ratio of 60, dry basis content of 90 wt%) was mixed with 41.70 kg of deionized water, 12.31 kg of kaolin, and 11.15 kg of pseudo-boehmite for 5 hours.
[0062](2) Add 0.93 kg of 35 wt% hydrochloric acid to the slurry in (1), and stir for 60 minutes.
[0063] (3) Add 2.22 kg of water glass to the acidified solution and stir for 30 minutes until uniform.
[0064] (4) Add 0.80 kg of phosphoric acid to the slurry in (3), and stir for 30 minutes until uniform.
[0065] (5) Add 3.6 kg of alkaline silica sol to the above acidified slurry and stir for about 30 minutes until uniform to obtain a catalyst slurry.
[0066] (6) The obtained catalyst slurry is spray-dried, washed with water and dried to obtain the catalyst SL-3.
PUM
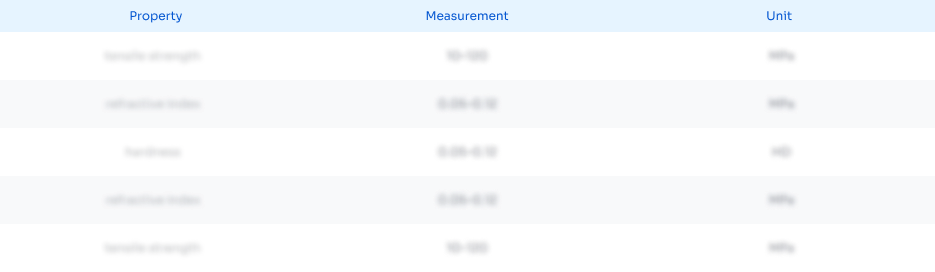
Abstract
Description
Claims
Application Information

- R&D
- Intellectual Property
- Life Sciences
- Materials
- Tech Scout
- Unparalleled Data Quality
- Higher Quality Content
- 60% Fewer Hallucinations
Browse by: Latest US Patents, China's latest patents, Technical Efficacy Thesaurus, Application Domain, Technology Topic, Popular Technical Reports.
© 2025 PatSnap. All rights reserved.Legal|Privacy policy|Modern Slavery Act Transparency Statement|Sitemap|About US| Contact US: help@patsnap.com