Photoelectric ceramic displacement closed loop servo control experimental device and control method
A photoelectric ceramics, closed-loop servo technology, applied in electrical program control, program control, digital control and other directions, can solve the problems of the drive control device and control method to be improved, the open-loop stage of photoelectric ceramic output displacement, and the inability to close-loop control, etc. The effect of avoiding program errors, increasing the scope, and improving the response speed
- Summary
- Abstract
- Description
- Claims
- Application Information
AI Technical Summary
Problems solved by technology
Method used
Image
Examples
Embodiment 1
[0034] combine figure 1, a photoelectric ceramic displacement closed-loop servo control experimental device of the present invention is suitable for the non-contact field of the micro-drive platform, especially suitable for the closed-loop servo control field of the output displacement of the photoelectric ceramic micro-driver. The experimental device includes a rough adjustment device for screw and nut pair, and a closed-loop servo control device for photoelectric ceramic displacement. Among them, the photoelectric ceramic 3, the photoelectric ceramic fixture 4, the platform column 14, the ultraviolet light source probe 15, and the optical shutter 16 in the photoelectric ceramic displacement closed-loop servo control device are located on the mobile platform 5 of the screw nut auxiliary coarse adjustment device.
[0035] combine figure 1 , figure 2 , the control method of a photoelectric ceramic displacement closed-loop servo control experimental device of the present inve...
PUM
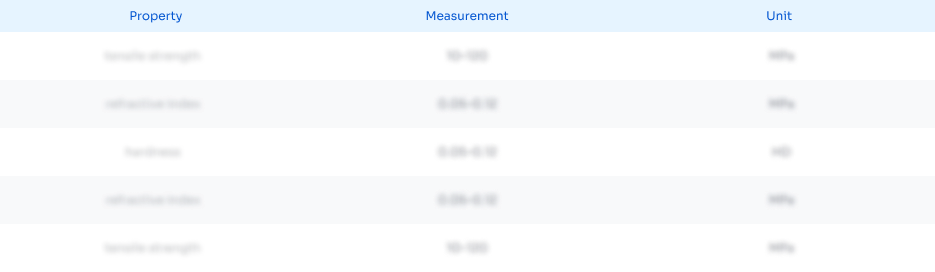
Abstract
Description
Claims
Application Information

- Generate Ideas
- Intellectual Property
- Life Sciences
- Materials
- Tech Scout
- Unparalleled Data Quality
- Higher Quality Content
- 60% Fewer Hallucinations
Browse by: Latest US Patents, China's latest patents, Technical Efficacy Thesaurus, Application Domain, Technology Topic, Popular Technical Reports.
© 2025 PatSnap. All rights reserved.Legal|Privacy policy|Modern Slavery Act Transparency Statement|Sitemap|About US| Contact US: help@patsnap.com