Preparation method of degradation controllable PLLA (poly-L-lactic acid)/PGA (poly glycolic acid) composite membrane
A technology of composite film and degradation time, which is applied in the field of PLLA/PGA composite film preparation, can solve the problems of inability, poor biocompatibility of mulch film, and poor compatibility of mixtures, etc.
- Summary
- Abstract
- Description
- Claims
- Application Information
AI Technical Summary
Problems solved by technology
Method used
Examples
Embodiment approach 1
[0014] (1) Weigh 450g PLLA and 50g PGA slices with a precision balance, then mix the slices and dry them in a vacuum drum, using a two-stage drying method, pre-crystallization before drying. First, the temperature is raised from room temperature to 65~70°C for 3~4 hours to pre-crystallize, and then the temperature is slowly raised to 110°C for 12 hours, so that the moisture content of the slices can be lower than 0.05%.
[0015] (2) Pass the dried slices through a twin-screw extruder to prepare composite slices. Set up 10 heating temperature zones for the twin-screw extruder: 1-2 zone 165~170°C, 3-4 zone 171-174°C, 5-6 zone 175-177°C, 7-8 zone 178-182°C, 9- Zone 10 185-190°C.
[0016] (3) Then dissolve the compound slices in the Erlenmeyer flask containing methylene chloride solution, adjust the water bath constant temperature oscillator to 25°C, and then put the Erlenmeyer flask into the water bath constant temperature oscillator, PLLA and PGA will slowly dissolve In dichlo...
Embodiment approach 2
[0021] (1) Weigh 250g PLLA and 250 PGA slices with a precision balance, then mix the slices and dry them in a vacuum drum, using a two-stage drying method, pre-crystallization before drying. First, the temperature is raised from room temperature to 65~70°C for 3~4 hours to pre-crystallize, and then the temperature is slowly raised to 110°C for 12 hours, so that the moisture content of the slices can be lower than 0.05%.
[0022] (2) Pass the dried slices through a twin-screw extruder to prepare composite slices. Set up 10 heating temperature zones for the twin-screw extruder: 1-2 zone 165~170°C, 3-4 zone 171-174°C, 5-6 zone 175-177°C, 7-8 zone 178-182°C, 9- Zone 10 185-190°C.
[0023] (3) Then dissolve the compound slices in the Erlenmeyer flask containing methylene chloride solution, adjust the water bath constant temperature oscillator to 25°C, and then put the Erlenmeyer flask into the water bath constant temperature oscillator, PLLA and PGA will slowly dissolve In dichlo...
Embodiment approach 3
[0028] (1) Weigh 50g PLLA and 450g PGA slices with a precision balance, then mix the slices and dry them in a vacuum drum, using a two-stage drying method, pre-crystallization before drying. First, the temperature is raised from room temperature to 65~70°C for 3~4 hours to pre-crystallize, and then the temperature is slowly raised to 110°C for 12 hours, so that the moisture content of the slices can be lower than 0.05%.
[0029] (2) Pass the dried slices through a twin-screw extruder to prepare composite slices. Set up 10 heating temperature zones for the twin-screw extruder: 1-2 zone 165~170°C, 3-4 zone 171-174°C, 5-6 zone 175-177°C, 7-8 zone 178-182°C, 9- Zone 10 185-190°C.
[0030] (3) Then dissolve the compound slices in the Erlenmeyer flask containing methylene chloride solution, adjust the water bath constant temperature oscillator to 25°C, and then put the Erlenmeyer flask into the water bath constant temperature oscillator, PLLA and PGA will slowly dissolve In dichlo...
PUM
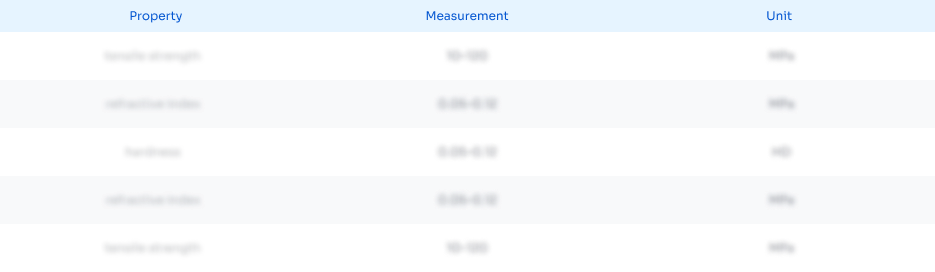
Abstract
Description
Claims
Application Information

- R&D
- Intellectual Property
- Life Sciences
- Materials
- Tech Scout
- Unparalleled Data Quality
- Higher Quality Content
- 60% Fewer Hallucinations
Browse by: Latest US Patents, China's latest patents, Technical Efficacy Thesaurus, Application Domain, Technology Topic, Popular Technical Reports.
© 2025 PatSnap. All rights reserved.Legal|Privacy policy|Modern Slavery Act Transparency Statement|Sitemap|About US| Contact US: help@patsnap.com