Automobile front axle production line and processing method
A technology of automobile front axle and processing method, which is applied in the direction of manufacturing tools and other manufacturing equipment/tools, etc., can solve the problems of uneven internal structure of the front axle, difficult forging process, and low performance indicators, so as to reduce manual labor and eliminate Effect of heat radiation and simplification of processing steps
- Summary
- Abstract
- Description
- Claims
- Application Information
AI Technical Summary
Problems solved by technology
Method used
Image
Examples
Embodiment 1
[0024] Example 1: Such as figure 1 As shown, the present invention provides an automobile front axle production line, including an automatic sawing machine 1, an intelligent intermediate frequency induction heating device 2, a forging and shaping device 4, a heat treatment intelligent automatic conveying device 7 and a closed environmental temperature heating and heat treatment device 8; the automatic The workpiece between the sawing machine 1, the intelligent intermediate frequency induction heating equipment 2 and the forging and shaping equipment 4 is transported by the intelligent robot arm 2.
Embodiment 2
[0025] Embodiment 2: As a further improvement to the automobile front axle production line of Embodiment 1, the intelligent intermediate frequency induction heating device 2 is provided with a double-layer heat preservation and heat insulation structure. The intelligent intermediate frequency induction heating device 2 includes a temperature closed-loop control system based on fuzzy neural network control. The intelligent intermediate frequency induction heating equipment 2 adopts a temperature closed-loop control system based on fuzzy neural network control technology. Compared with traditional PID and other control methods, it has high temperature control accuracy, strong reliability, high heating efficiency, fast speed, and no preheating. And other advantages, it can also shorten the auxiliary time and increase the production efficiency by 1.6 times. At the same time, the energy efficiency is high, and the energy consumption is reduced without any pollution. The forging and ...
Embodiment 3
[0026] Example 3: Such as figure 2 As shown, as a further improvement to the automobile front axle production line of embodiment 1, the closed environmental temperature heating and heat treatment equipment 8 of the automobile front axle production line further includes a hook type shot blasting machine 9 and a magnetic particle flaw detector 10 arranged in sequence. , Hydraulic straightening machine 11 and pneumatic spraying machine 12, the closed environmental temperature heating and heat treatment equipment 8, hook shot blasting machine 9, magnetic particle flaw detector 10, hydraulic straightening machine 11 and pneumatic spraying machine 12 between the workpiece by intelligent Robot arm 2 for transportation.
[0027] The invention also provides a method for processing the front axle of an automobile, such as image 3 As shown, the method includes the following steps: blanking, heating, rolling, bending, pre-forging, final forging, trimming, correction, heat treatment, shot b...
PUM
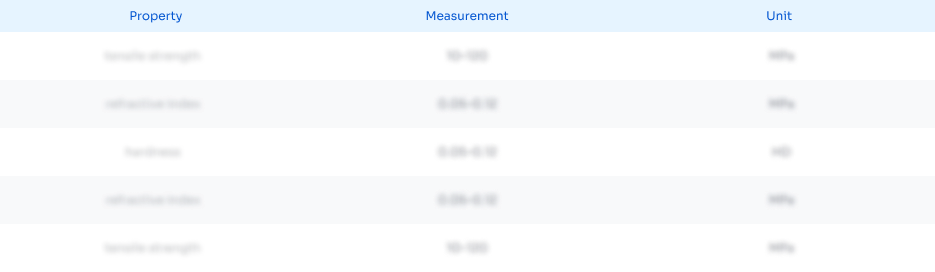
Abstract
Description
Claims
Application Information

- Generate Ideas
- Intellectual Property
- Life Sciences
- Materials
- Tech Scout
- Unparalleled Data Quality
- Higher Quality Content
- 60% Fewer Hallucinations
Browse by: Latest US Patents, China's latest patents, Technical Efficacy Thesaurus, Application Domain, Technology Topic, Popular Technical Reports.
© 2025 PatSnap. All rights reserved.Legal|Privacy policy|Modern Slavery Act Transparency Statement|Sitemap|About US| Contact US: help@patsnap.com