Method for preparing lithium carbonate by employing discarded lithium iron phosphate battery
A lithium iron phosphate battery and lithium carbonate technology, applied in lithium carbonate;/acid carbonate, battery recovery, recycling technology, etc., can solve the problem of low purity of lithium carbonate, low extraction efficiency, and high loss of lithium And other issues
- Summary
- Abstract
- Description
- Claims
- Application Information
AI Technical Summary
Problems solved by technology
Method used
Image
Examples
Embodiment 1
[0036] A method for reclaiming and preparing lithium carbonate from scrapped lithium iron phosphate battery positive plates, comprising the following steps:
[0037] (1) Use a crusher to crush the scrapped positive electrode sheet into a block positive electrode sheet smaller than 6cm;
[0038] (2) Calcining the block-shaped positive electrode sheet at 600°C for 1 hour in a high-temperature furnace with a nitrogen atmosphere;
[0039] (3) Use vibrating sieve to vibrate and separate the calcined block positive electrode sheet to obtain positive electrode material and recycled aluminum foil;
[0040] (4) Grinding the obtained positive electrode material with a grinder until the particle size is below 75 μm;
[0041] (5) After grinding, the positive electrode material was mixed with 5mol / L sulfuric acid solution at a solid-to-liquid ratio of 1:6 (g:ml), and stirred and reacted at 70°C for 3 hours;
[0042] (6) Add a TOPO-kerosene extraction system with a volume ratio of 1:1 to ...
Embodiment 2
[0045] A method for reclaiming and preparing lithium carbonate from scrapped lithium iron phosphate battery positive plates, comprising the following steps:
[0046] (1) Use a crusher to crush the scrapped positive electrode sheet into a block positive electrode sheet smaller than 6cm;
[0047] (2) Calcinate the block-shaped positive electrode sheet at 500°C for 2 hours in a high-temperature furnace with a nitrogen atmosphere;
[0048] (3) Use vibrating sieve to vibrate and separate the calcined block positive electrode sheet to obtain positive electrode material and recycled aluminum foil;
[0049] (4) Grinding the obtained positive electrode material with a grinder until the particle size is below 75 μm;
[0050] (5) After grinding, the positive electrode material was mixed with 3mol / L sulfuric acid solution at a solid-to-liquid ratio of 1:12 (g:ml), and stirred and reacted at 90°C for 1 hour;
[0051] (6) Add TOPO-kerosene extraction system with a volume ratio of 3:1 to t...
Embodiment 3
[0054] A method for reclaiming and preparing lithium carbonate from scrapped lithium iron phosphate battery positive plates, comprising the following steps:
[0055] (1) Use a crusher to crush the scrapped positive electrode sheet into a block positive electrode sheet smaller than 6cm;
[0056] (2) Calcinate the block-shaped positive electrode sheet at 400°C for 3 hours in a high-temperature furnace with a nitrogen atmosphere;
[0057] (3) Use vibrating sieve to vibrate and separate the calcined block positive electrode sheet to obtain positive electrode material and recycled aluminum foil;
[0058](4) Grinding the obtained positive electrode material with a grinder until the particle size is below 75 μm;
[0059] (5) After grinding, the positive electrode material was mixed with 1mol / L sulfuric acid solution at a solid-to-liquid ratio of 1:15 (g:ml), and stirred and reacted at 80°C for 2 hours;
[0060] (6) Add a TOPO-kerosene extraction system with a volume ratio of 2:1 to...
PUM
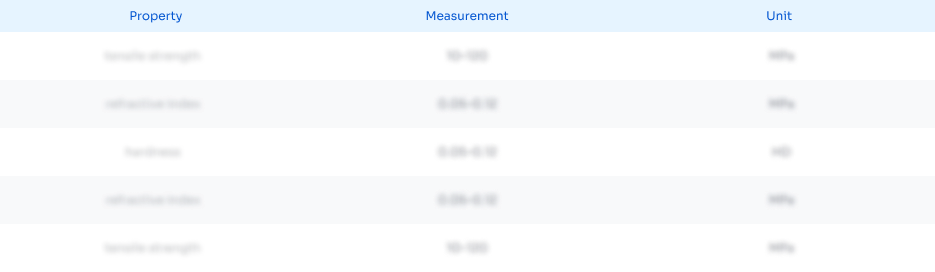
Abstract
Description
Claims
Application Information

- Generate Ideas
- Intellectual Property
- Life Sciences
- Materials
- Tech Scout
- Unparalleled Data Quality
- Higher Quality Content
- 60% Fewer Hallucinations
Browse by: Latest US Patents, China's latest patents, Technical Efficacy Thesaurus, Application Domain, Technology Topic, Popular Technical Reports.
© 2025 PatSnap. All rights reserved.Legal|Privacy policy|Modern Slavery Act Transparency Statement|Sitemap|About US| Contact US: help@patsnap.com