Multi-rotor unmanned aerial vehicle detection platform system for detecting surface cracks of structural member and method for detecting surface cracks of structural member with multi-rotor unmanned aerial vehicle detection platform system
A multi-rotor UAV and surface cracking technology, which is applied in control/adjustment system, aircraft parts, position/direction control, etc., can solve the problems of heavy weight, low degree of automation, high price, etc., to reduce detection costs and improve The degree of automation and the effect of saving working time
- Summary
- Abstract
- Description
- Claims
- Application Information
AI Technical Summary
Problems solved by technology
Method used
Image
Examples
Embodiment 1
[0088] A multi-rotor UAV inspection platform system for detecting cracks on the surface of structural parts.
[0089] Such as figure 1 As shown, the multi-rotor UAV inspection platform system includes multi-rotor UAV I for providing task loads and detecting cracks on the surface of structural parts, and a control system for controlling the movement of multi-rotor UAV I and performing crack detection operations Ⅱ and wireless communication system Ⅲ for transmitting remote control commands and sensing information;
[0090] The multi-rotor UAV I for providing task loads and detecting cracks on the surface of structural parts includes a body 11 that provides a physical installation interface and a support frame for the equipment, a power system 12 that provides lift and motion for the body 11, and is used for positioning 1. A sensor system 13 for adjusting flight attitude and detecting cracks on the surface of structural parts;
[0091] The body 11 includes: a frame 111, a trip...
Embodiment 2
[0115] A method of detecting cracks on the surface of a structural member.
[0116] It is a method for detecting cracks on the surface of structural parts by the multi-rotor drone detection platform system for detecting cracks on the surface of structural parts described in the first embodiment. The device and the ranging sensor establish a stable proportional relationship between the actual object scale and the number of image pixels, and obtain the actual size of the crack by counting the pixels occupied by the crack on the image; the specific steps (see image 3 )yes:
[0117] A. According to the type of target to be measured, select the installation method of the pan / tilt, install a fixed camera and a distance sensor:
[0118] If the target to be measured is above the UAV, use the upper installation of the pan / tilt, that is: install the pan / tilt 114 and the camera 134 above the body 11 of the multi-rotor UAV, otherwise use the lower installation, that is: install the pan / ...
Embodiment 2
[0152] The second method of embodiment two is used:
[0153] Apply the "multi-rotor UAV detection platform system for detecting cracks on the surface of structural parts" described in Example 1 to "detection of the appearance of the bridge floor. The main purpose of the detection is to find cracks with a maximum width greater than 0.2mm, and give The position of the crack is convenient for maintenance and remediation, that is, the detection accuracy P To be better than 0.2mm, test by 0.15mm / pix; its method is the same as the basic steps of embodiment two, and one of the differences with the method of embodiment two is that in D, the unmanned aerial vehicle flies by the preset route autonomously, And in the step of extracting the image of the target to be inspected, there is a difference in the way of obtaining the image of the structural part. The image is taken after the drone hovers and stabilizes. The specific steps are as follows:
[0154] A. According to the type of targ...
PUM
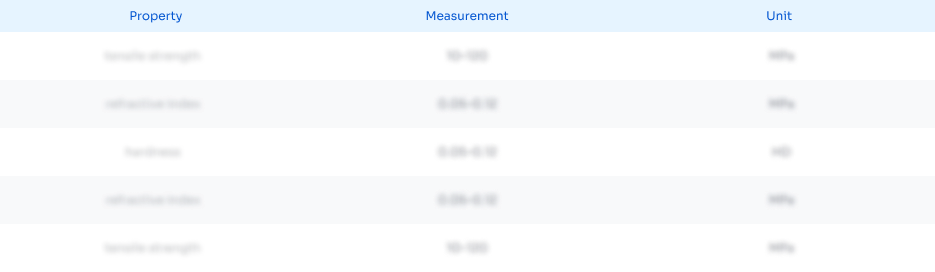
Abstract
Description
Claims
Application Information

- R&D
- Intellectual Property
- Life Sciences
- Materials
- Tech Scout
- Unparalleled Data Quality
- Higher Quality Content
- 60% Fewer Hallucinations
Browse by: Latest US Patents, China's latest patents, Technical Efficacy Thesaurus, Application Domain, Technology Topic, Popular Technical Reports.
© 2025 PatSnap. All rights reserved.Legal|Privacy policy|Modern Slavery Act Transparency Statement|Sitemap|About US| Contact US: help@patsnap.com