Thermoplastic continuous fiber composite material and preparation method thereof and production device
A continuous fiber and composite material technology, which is applied in the field of thermoplastic continuous fiber composite materials and its preparation, can solve the problems of hindering the adhesion of the thermoplastic film layer and the fiber fabric, the thermoplastic film porosity is small, and the extrusion device is easily damaged, and achieves excellent performance. Liquid permeability, improved interlayer adhesion, and simple device composition
- Summary
- Abstract
- Description
- Claims
- Application Information
AI Technical Summary
Problems solved by technology
Method used
Image
Examples
Embodiment 1
[0035] This embodiment provides a method for preparing a thermoplastic continuous fiber composite material, which specifically includes the following steps:
[0036] (1) Under the condition of 200°C, the polypropylene particles are heated and melted by a screw extruder to form a melt, and the melt is extruded from the extruder and output to the melt injection die, and then to the Hot air is introduced into the cavity of the melt injection die, so that the melt is ejected from the cavity of the melt injection die under negative pressure to form melt blown fibers, and a part of the obtained Melt-blown fibers are processed by hot rolling to obtain thermoplastic non-woven fabrics made of polypropylene; a part of the melt-blown fibers prepared is made into a 3-dimensional woven fiber fabric; the other part is used as Z-direction reinforcing fibers;
[0037] (2) The fiber fabric is laid between two adjacent layers of the polypropylene thermoplastic non-woven fabric, and the prefabri...
Embodiment 2
[0041] This example provides a method for preparing a thermoplastic continuous fiber composite material, the steps of which are roughly the same as those in Example 1, except that:
[0042] The step (1) also includes spraying nanomaterials on one side of the thermoplastic nonwoven fabric made of polyethylene with a spraying machine at a temperature of 150°C to form a nanomaterial layer, and the nanomaterials can be alumina , zinc oxide, copper oxide, nano-carbon black, carbon nanofibers, carbon nanofibers, nano-graphene, nano-clay tubes, etc.
[0043] The polyethylene continuous fiber composite material prepared by the preparation method of the thermoplastic continuous fiber composite material provided in this embodiment has an eight-layer structure, and the specific structure is as follows image 3 As shown, it includes three layers of thermoplastic non-woven fabric layer 1 made of polyethylene material, and the surface of one side of the thermoplastic non-woven fabric layer ...
Embodiment 3
[0046] This example provides a method for preparing a thermoplastic continuous fiber composite material, the steps of which are roughly the same as those in Example 1, except that:
[0047] The raw material that present embodiment adopts is the combination of TPU and PA6;
[0048] The step (2) also includes the sub-step of using a spraying machine to spray nanomaterials on the surface of the preform at a temperature of 150°C, and the nanomaterials can be aluminum oxide, zinc oxide, copper oxide, etc.
[0049] The thermoplastic continuous fiber composite material prepared by the preparation method of the thermoplastic continuous fiber composite material provided in this example has a seven-layer structure, and the specific structure is as follows Figure 5 As shown, it includes three layers of thermoplastic non-woven fabric layers 1 made of polyethylene, and a layer of carbon fiber fabric 2 is laid between two adjacent layers of thermoplastic non-woven fabric layers 1 made of p...
PUM
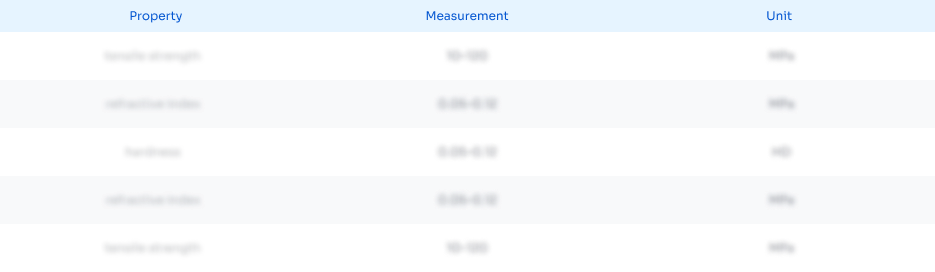
Abstract
Description
Claims
Application Information

- Generate Ideas
- Intellectual Property
- Life Sciences
- Materials
- Tech Scout
- Unparalleled Data Quality
- Higher Quality Content
- 60% Fewer Hallucinations
Browse by: Latest US Patents, China's latest patents, Technical Efficacy Thesaurus, Application Domain, Technology Topic, Popular Technical Reports.
© 2025 PatSnap. All rights reserved.Legal|Privacy policy|Modern Slavery Act Transparency Statement|Sitemap|About US| Contact US: help@patsnap.com