Method for preparing slow-release fertilizer coating from fermentation residues of wood fibers for ethanol production and application
A technology of ethanol fermentation and slow-release fertilizers, which is applied in application, fertilizer mixture, layered/coated fertilizers, etc., can solve the problems of complex process, high cost, secondary pollution of soil, etc., and achieve simple preparation method, low cost, Effect of improving soil properties
- Summary
- Abstract
- Description
- Claims
- Application Information
AI Technical Summary
Problems solved by technology
Method used
Image
Examples
Embodiment 1
[0036] The lignocellulosic ethanol fermentation residue is dried and pulverized, and passed through a 100-mesh sieve for later use. Take 20g of dried and pulverized lignocellulosic ethanol fermentation residue and put it into a 500mL three-neck flask, add 80mL of pure water for mixing, use NaOH solution to adjust the pH to 8.0, and place it in an ultrasonic cleaner for 6 hours.
[0037] Add 5 g of acetic anhydride to a three-neck flask containing the solution of lignocellulosic ethanol fermentation residue, and mechanically stir for 6 hours in a constant temperature water bath at 90°C.
[0038] Slowly add 10 g of polyvinyl alcohol (AH-26, alcoholysis degree: 98%) into 90 mL of pure water, stir rapidly while adding, and gradually raise the temperature from room temperature to 40°C.
[0039] The polyvinyl alcohol solution is slowly added dropwise to the lignocellulosic ethanol fermentation residue and the acetic anhydride solution, in a water bath at 90° C., and mechanically sti...
Embodiment 2
[0041] The lignocellulosic ethanol fermentation residue is dried and pulverized, and passed through a 100-mesh sieve for later use. Take 20g of dried and pulverized lignocellulosic ethanol fermentation residue and put it into a 500mL three-neck flask, add 80mL of pure water for mixing, use NaOH solution to adjust the pH to 8.0, and place it in an ultrasonic cleaner for 6 hours.
[0042] In the three-necked flask containing the residue solution of lignocellulosic ethanol fermentation, 5 g of formaldehyde solution was slowly added dropwise, and mechanically stirred for 6 hours in a constant temperature water bath at 90°C.
[0043] Slowly add 10 g of polyvinyl alcohol (AH-26, alcoholysis degree: 98%) into 90 mL of pure water, stir rapidly while adding, and gradually raise the temperature from room temperature to 40°C.
[0044] The polyvinyl alcohol solution is slowly added dropwise to the residue of lignocellulosic ethanol fermentation and formaldehyde solution, in a 90° C. water...
Embodiment 3
[0046]The lignocellulosic ethanol fermentation residue is dried and pulverized, and passed through a 100-mesh sieve for later use. Take 20g of dried and pulverized lignocellulosic ethanol fermentation residue and put it into a 500mL three-neck flask, add 80mL of pure water for mixing, use NaOH solution to adjust the pH to 8.0, and place it in an ultrasonic cleaner for 6 hours.
[0047] Add 5 g of citric anhydride to a three-necked flask containing a solution of lignocellulosic ethanol fermentation residue, and mechanically stir for 6 hours in a constant temperature water bath at 90°C.
[0048] Slowly add 10 g of polyvinyl alcohol (AH-26, alcoholysis degree: 98%) into 90 mL of pure water, stir rapidly while adding, and gradually raise the temperature from room temperature to 40°C.
[0049] The polyvinyl alcohol solution is slowly added dropwise to the lignocellulosic ethanol fermentation residue and citric anhydride solution, in a 90° C. water bath, and mechanically stirred for...
PUM
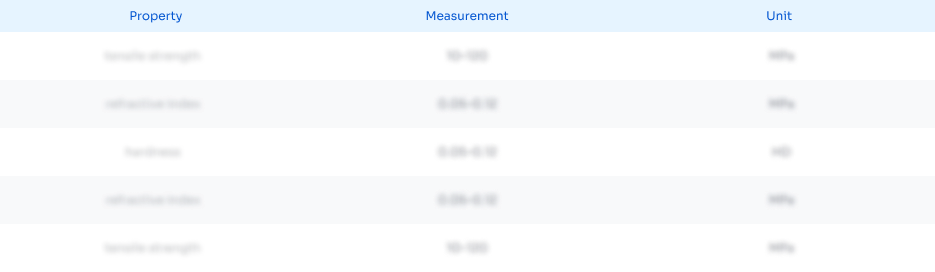
Abstract
Description
Claims
Application Information

- Generate Ideas
- Intellectual Property
- Life Sciences
- Materials
- Tech Scout
- Unparalleled Data Quality
- Higher Quality Content
- 60% Fewer Hallucinations
Browse by: Latest US Patents, China's latest patents, Technical Efficacy Thesaurus, Application Domain, Technology Topic, Popular Technical Reports.
© 2025 PatSnap. All rights reserved.Legal|Privacy policy|Modern Slavery Act Transparency Statement|Sitemap|About US| Contact US: help@patsnap.com