Cold application water-blocking type optical power cable filling past and production method thereof
A technology for filling paste and optical cables, applied in the direction of insulating cables, cables, circuits, etc., can solve the problems of affecting the electrical conductivity of cables, stress concentration, loss of filling paste, etc., achieve good water blocking effect, good water absorption effect, and reduce production costs Effect
- Summary
- Abstract
- Description
- Claims
- Application Information
AI Technical Summary
Problems solved by technology
Method used
Examples
Embodiment 1
[0024] Pour 60g of hydrogenated white oil and 10g of lubricating oil into the kettle and heat it to 70°C, then add 0.6g of phenolic antioxidant and 4.5g of alkylphenol polyoxyethylene ether emulsifier into it in sequence , and 7.8g of water-blocking agent, fully stirred for 5 hours, and after the whole liquid was completely emulsified, it was rapidly cooled to room temperature by cooling equipment, and then added to the cooled mixed liquid was an additive composed of 6g of white carbon black and 2g of diatomaceous earth. Thickener, and 0.6g fatty acid lipid dispersant, stirred evenly for 0.5 hours, and finally added 8.5g cross-linked sodium polyacrylate synthetic polymer water-absorbent resin to the evenly stirred mixed solution, and after uniform stirring, the mixed solution was pumped into the mixed solution by a vacuum pump. The air bubbles are pumped out, and the mixture is poured out of the container after the pumping is complete.
Embodiment 2
[0026] Pour 75g of base oil of synthetic olefin oil into the kettle and heat it to 80°C, then add 0.2g of phenolic antioxidant and 0.3g of aniline antioxidant to it, and 3.5g of benzene Ethylphenol polyoxyethylene ether emulsifier, and 8g water blocking agent, fully stirred for 5.5 hours, after the whole liquid was completely emulsified, it was quickly cooled to room temperature through cooling equipment, and then 5g bentonite was added to the cooled mixture to thicken dispersant, and 0.5g of paraffin wax dispersant, stirred evenly for 0.8 hours, and finally added 7.5g of polymer water-absorbent resin synthesized by polyacrylonitrile resin to the uniformly stirred mixed solution, and after uniformly stirred, the air bubbles in the mixed solution were removed by a vacuum pump Take it out, and pour the mixture out of the container after the pumping is complete.
Embodiment 3
[0028] Pour 80g of hydrogenated white oil base oil into the kettle and heat it to 90°C, then add 0.2g of phosphite triester antioxidant, 2g of fatty alcohol polyoxyethylene ether emulsifier, and 8.5g of retarder Aqua, fully stirred for 6 hours, after the whole liquid is completely emulsified, it is rapidly cooled to room temperature by cooling equipment, and then 3g of diatomite thickener and 0.3g of paraffin wax dispersant are added to the cooled mixed solution to carry out uniform Stir for 1 hour, and finally add 6g of polymer water-absorbent resin synthesized by polyacrylonitrile resin to the uniformly stirred mixed solution, and after uniform stirring, the air bubbles in the mixed solution are extracted by a vacuum pump, and the mixed solution is poured out after the exhaust is completed. out of the container.
[0029] The index parameters of the above embodiments are as follows:
[0030] technical indicators standard Embodiment one Embodiment two Embodim...
PUM
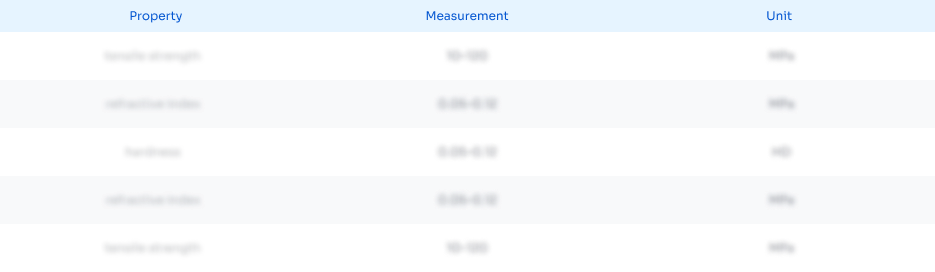
Abstract
Description
Claims
Application Information

- R&D
- Intellectual Property
- Life Sciences
- Materials
- Tech Scout
- Unparalleled Data Quality
- Higher Quality Content
- 60% Fewer Hallucinations
Browse by: Latest US Patents, China's latest patents, Technical Efficacy Thesaurus, Application Domain, Technology Topic, Popular Technical Reports.
© 2025 PatSnap. All rights reserved.Legal|Privacy policy|Modern Slavery Act Transparency Statement|Sitemap|About US| Contact US: help@patsnap.com