A clean production process for amino acids such as iminodiacetic acid
A technology of iminodiacetic acid and iminodiacetic acid calcium, which is applied in the fields of chemical fertilizers, fine chemicals, and pesticides, can solve the problems of complex refining process, poor salt quality, and many times of solid-liquid separation, so as to simplify the process steps and reduce production Cost, the effect of achieving cleaner production
- Summary
- Abstract
- Description
- Claims
- Application Information
AI Technical Summary
Problems solved by technology
Method used
Image
Examples
Embodiment 1
[0039] Example 1 Preparation of calcium iminodiacetate by hydrolyzing iminodiacetonitrile with milk of lime
[0040] Lime (31.4 g, 98%, 0.55 mol) was added to water (200 g), and stirred for 15 min. Keep the temperature of the solution at about 50°C, add iminodiacetonitrile (50 g, 95%, 0.5 mol) in portions, and complete the addition in about half an hour. Stir at 50-55°C for 0.5-1 h, raise the temperature to about 90-100°C, deamination under reduced pressure, and replenish water in due time. When the pH of the evaporated water vapor is 8-9, stop the deamination. The solution was filtered and washed.
[0041] The crude product of calcium iminodiacetic acid (113 g, containing iminodiacetic acid: 58 g, 1 No other impurities were found on H-NMR), the filtrate was combined with washing liquid (containing iminodiacetic acid: 5.2 g), and the total yield of iminodiacetic acid calcium was 95.0%.
Embodiment 2
[0042] Example 2 Calcium iminodiacetate was prepared by hydrolyzing iminodiacetonitrile with milk of lime, and the mother liquor was applied mechanically
[0043] Put lime (31.4 g, 98%, 0.55 mol) into water (60 g), stir and react for 15 min, and then add the mother liquor from the previous batch of calcium salt separation. Keep the temperature of the solution at about 50°C, add iminodiacetonitrile (50 g, 95%, 0.5 mol) in portions, and complete the addition in about half an hour. Stir at 50-55°C for 0.5-1 h, raise the temperature to about 90-100°C, deamination under reduced pressure, and replenish water in due time. When the pH of the evaporated water vapor is 8-9, stop the deamination. The calcium iminodiacetic acid was filtered out, washed, washed with water and combined with mother liquor for the next batch of reactions.
[0044] The experimental results are as follows, the total yield of iminodiacetic acid in the crude product of 7 batches of reaction iminodiacetic acid ca...
Embodiment 3
[0046] Example 3 Patent (publication number: CN101619077A) method to prepare calcium iminodiacetate
[0047] Add 872 mL of water to the reactor, evacuate to 0.1 Mpa, raise the temperature to 45-50°C, add lime (70%, 143 g) and iminodiacetonitrile (95%, 151 g) into the water several times evenly, each Add once every 5 minutes, finish adding in 3 hours, keep warm for 1 hour, then raise the temperature to 75°C, keep warm for 2 hours, then raise the temperature to 100°C, keep warm for reaction, stop the reaction when the pH of the water vapor is 7, cool, filter, The filtrate and filter cake were collected separately.
[0048] The crude product of calcium iminodiacetic acid (117 g, containing iminodiacetic acid: 58.8 g, impurities: nitrilotriacetic acid: 3.8 g, glycine: 0.1 g) was obtained in the experiment, and the filtrate was combined with washing liquid (containing iminodiacetic acid: 3.53 g ), the total yield of iminodiacetic acid was 93.8%.
[0049] Compared with Example 1, ...
PUM
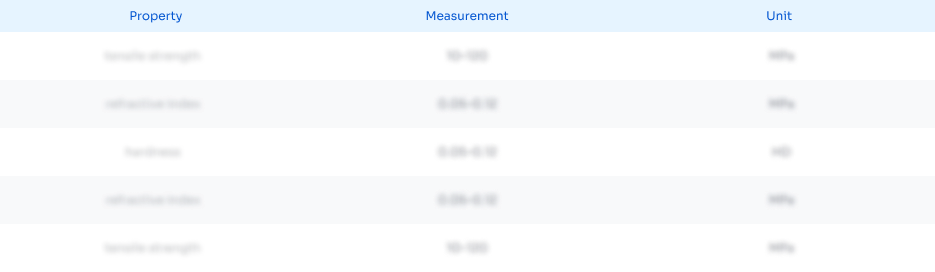
Abstract
Description
Claims
Application Information

- R&D
- Intellectual Property
- Life Sciences
- Materials
- Tech Scout
- Unparalleled Data Quality
- Higher Quality Content
- 60% Fewer Hallucinations
Browse by: Latest US Patents, China's latest patents, Technical Efficacy Thesaurus, Application Domain, Technology Topic, Popular Technical Reports.
© 2025 PatSnap. All rights reserved.Legal|Privacy policy|Modern Slavery Act Transparency Statement|Sitemap|About US| Contact US: help@patsnap.com