Steam power cycle thermal power generation system and steam power cycle thermal generation technology
A technology for thermal power generation and steam power, applied in the field of boilers, can solve the problems of poor thermodynamics, increased exhaust gas temperature, and unadjustable, so as to avoid the limitation of temperature difference pinch points and reduce the power consumption of fans
- Summary
- Abstract
- Description
- Claims
- Application Information
AI Technical Summary
Problems solved by technology
Method used
Image
Examples
Embodiment Construction
[0016] see figure 1 As shown, a steam power cycle thermal power generation system of the present invention includes a furnace and a boiler high-temperature flue gas section 1, a first reheater 5, a second reheater 6, a superheater 7, a water wall 8, and a main steam pipeline 9 , generator 10, steam turbine 12, condenser 14, condensate pump 16, high pressure condensate pump 17, flue gas purification system 18, high pressure condensate heater 19, fan 20, low pressure heater 22, feed water pump 23 and high pressure heater twenty four.
[0017] The boiler high-temperature flue gas section of the furnace 1 is equipped with a first reheater 5, a second reheater 6, a superheater 7 and a water-cooled wall 8; Theoretically speaking, the flue gas above the average endothermic temperature belongs to the high temperature flue gas. The first reheater 5 and the second reheater 6 are connected to the reheat steam inlet and outlet 11 of the steam turbine through pipelines. The outlet of th...
PUM
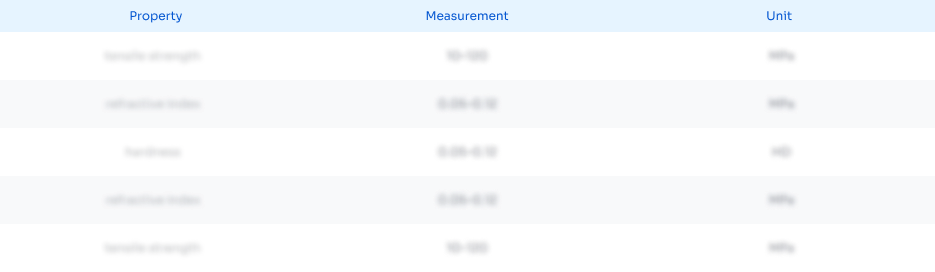
Abstract
Description
Claims
Application Information

- R&D
- Intellectual Property
- Life Sciences
- Materials
- Tech Scout
- Unparalleled Data Quality
- Higher Quality Content
- 60% Fewer Hallucinations
Browse by: Latest US Patents, China's latest patents, Technical Efficacy Thesaurus, Application Domain, Technology Topic, Popular Technical Reports.
© 2025 PatSnap. All rights reserved.Legal|Privacy policy|Modern Slavery Act Transparency Statement|Sitemap|About US| Contact US: help@patsnap.com