Acrylate adhesive, preparation method thereof and adhesive for engineering-level reflective film
A technology of acrylate and butyl acrylate, applied in the direction of ester copolymer adhesives, polymer adhesive additives, adhesive types, etc., can solve the problem of weak adhesion and limited application range of engineering-grade reflective films and other problems, to achieve excellent adhesion, outstanding water resistance, and good adhesion performance
- Summary
- Abstract
- Description
- Claims
- Application Information
AI Technical Summary
Problems solved by technology
Method used
Examples
Embodiment 1
[0023] 1) Weigh 17.6 parts of butyl acrylate, 0.3 parts of acrylic acid, 20 parts of methyl isobutyl ketone, 20 parts of ethyl acetate, 0.04 parts of azobisisobutyronitrile, and 8 parts of tackifying resin in parts by weight, and set aside;
[0024] 2) Mix butyl acrylate and acrylic acid to obtain a monomer mixture;
[0025] 3) Add 4.5 parts of monomer mixture, 8.9 parts of ethyl acetate, and 0.001 parts of azobisisobutyronitrile into the reaction kettle;
[0026] 4) Add in the high-level monomer dropping tank: 13.4 parts of monomer mixture, 0.2 parts of ethyl acetate;
[0027] 5) Add 0.039 parts of azobisisobutyronitrile and 7.4 parts of ethyl acetate into the high-level catalyst dropping tank;
[0028] 6) Heat the material in the reactor to reflux and react for 20 minutes in a foaming state, start to drop the raw materials in the high-level monomer dropping tank for 80 minutes; at the same time, drop the raw materials in the high-level catalyst dropping tank for 90 minutes ...
Embodiment 2
[0031] 1) Weigh 23 parts of butyl acrylate, 0.5 part of acrylic acid, 0.2 part of hydroxyethyl acrylate, 25 parts of methyl isobutyl ketone, 26 parts of ethyl acetate, 0.06 part of azobisisobutyronitrile, 10 parts viscose resin, set aside;
[0032] 2) Mix butyl acrylate, acrylic acid and hydroxyethyl acrylate to obtain a monomer mixture;
[0033] 3) Add 5.9 parts of monomer mixture, 11.5 parts of ethyl acetate, and 0.001 parts of azobisisobutyronitrile into the reactor;
[0034] 4) Add in the high-level monomer dropping tank: 17.8 parts of monomer mixture, 0.28 parts of ethyl acetate;
[0035] 5) Add 0.059 parts of azobisisobutyronitrile and 9.6 parts of ethyl acetate into the high-level catalyst dropping tank;
[0036] 6) Heat the material in the reactor to reflux and react in a foaming state for 22 minutes, start to drop the raw materials in the high-level monomer dropping tank for 85 minutes at a constant speed; at the same time, drop the raw materials in the high-level c...
Embodiment 3
[0039] 1) Weigh 28 parts of butyl acrylate, 0.7 part of acrylic acid, 0.4 part of hydroxyethyl acrylate, 30 parts of methyl isobutyl ketone, 32 parts of ethyl acetate, 0.08 part of azobisisobutyronitrile, 13 parts viscose resin, set aside;
[0040] 2) Mix butyl acrylate, acrylic acid and hydroxyethyl acrylate to obtain a monomer mixture;
[0041] 3) Add 7.3 parts of monomer mixture, 14 parts of ethyl acetate, and 0.002 parts of azobisisobutyronitrile into the reactor;
[0042] 4) Add in the high-level monomer dropping tank: 21.8 parts of monomer mixture, 0.3 parts of ethyl acetate;
[0043] 5) Add 0.078 parts of azobisisobutyronitrile and 12 parts of ethyl acetate into the high-level catalyst dropping tank;
[0044] 6) Heat the material in the reactor to reflux and react in a foaming state for 25 minutes, start to drop the raw materials in the high-level monomer dropping tank for 90 minutes at a constant speed; at the same time, drop the raw materials in the high-level catal...
PUM
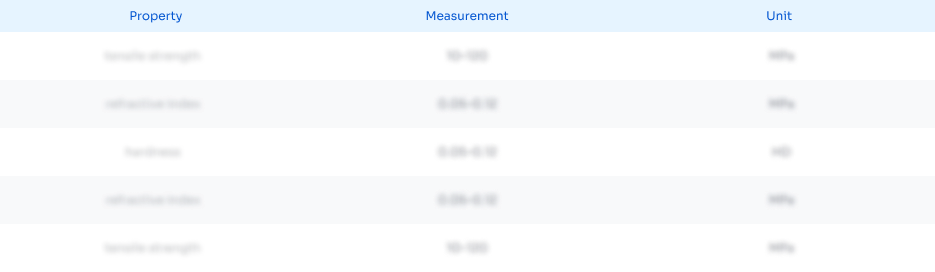
Abstract
Description
Claims
Application Information

- R&D Engineer
- R&D Manager
- IP Professional
- Industry Leading Data Capabilities
- Powerful AI technology
- Patent DNA Extraction
Browse by: Latest US Patents, China's latest patents, Technical Efficacy Thesaurus, Application Domain, Technology Topic, Popular Technical Reports.
© 2024 PatSnap. All rights reserved.Legal|Privacy policy|Modern Slavery Act Transparency Statement|Sitemap|About US| Contact US: help@patsnap.com