O-diallyl bisphenol a diglycidyl ether and its preparation process and application
A technology of ortho-diallyl bisphenol and diglycidyl ether, applied in the field of ortho-diallyl bisphenol A diglycidyl ether and its preparation process and application, capable of solving limitations, brittleness, impact resistance and stress Poor cracking ability and other problems, to achieve the effect of low equipment requirements, easy control of reaction, and stable process
- Summary
- Abstract
- Description
- Claims
- Application Information
AI Technical Summary
Problems solved by technology
Method used
Image
Examples
preparation example Construction
[0038] The preparation technology of o-diallyl bisphenol A diglycidyl ether, the reaction scheme is as follows:
[0039]
[0040] Brief description of the reaction route: o-diallyl bisphenol A and epichlorohydrin, under the catalysis of the catalyst triethylbenzyl ammonium chloride, under the condition of dropping liquid alkali, react to form o-diallyl Bisphenol A diglycidyl ether.
[0041] Process flow chart for the preparation of o-diallyl bisphenol A diglycidyl ether: as figure 1 shown.
[0042] The preparation process steps of the present invention are: feeding materials, etherification, adding alkali to keep warm, recovering epichlorohydrin, adding solvent, standing and separating, washing to neutrality, recovering solvent, and discharging.
Embodiment 1
[0044] (1) Feeding: Add 10.0kg of o-diallyl bisphenol A, 100g of catalyst triethylbenzyl ammonium chloride, and 6.82kg of epichlorohydrin into a 50L enamel reaction kettle in sequence, close the feeding port, and start stirring . The molar ratio of o-diallyl bisphenol A to epichlorohydrin is 1:2.5.
[0045] (2) Etherification: Slowly raise the temperature to 60°C, start timing, and keep warm for 4 hours in the range of 60-70°C.
[0046] (3) Alkali addition: cool down to 45-50°C, use a high-temperature tank, drop 8.39kg of liquid caustic soda with a concentration of 32%, control the rate of addition, and complete the addition within 1.5 hours. The molar ratio of o-diallyl bisphenol A to sodium hydroxide in liquid caustic soda is 1:2.3.
[0047] (4) Heat preservation: Slowly raise the temperature to 60°C, start timing, and keep the temperature within the range of 65-80°C for 5 hours.
[0048] (5) Recovery of epichlorohydrin: Distill at atmospheric pressure to 118°C first, the...
Embodiment 2
[0055] (1) Feeding: Add 10.0kg of o-diallyl bisphenol A, 150g of catalyst triethylbenzyl ammonium chloride, and 7.64kg of epichlorohydrin into a 50L enamel reaction kettle in sequence, after closing the feeding port, start stirring . The molar ratio of o-diallyl bisphenol A to epichlorohydrin is 1:2.8.
[0056] (2) Etherification: Slowly raise the temperature to 60°C, start timing, and keep warm for 5 hours in the range of 70-80°C.
[0057] (3) Alkali addition: the temperature is lowered to 45-50° C., and using the overhead tank, 9.12 kg of liquid caustic soda with a concentration of 32% is added dropwise, and the drop rate is controlled, and the dropwise addition is completed within 1.5 hours. The molar ratio of o-diallyl bisphenol A to sodium hydroxide in liquid caustic soda is 1:2.5.
[0058] (4) Heat preservation: Slowly raise the temperature to 60°C, start timing, and keep heat in the range of 65-70°C for 10 hours.
[0059] (5) Recovery of epichlorohydrin: Distill at a...
PUM
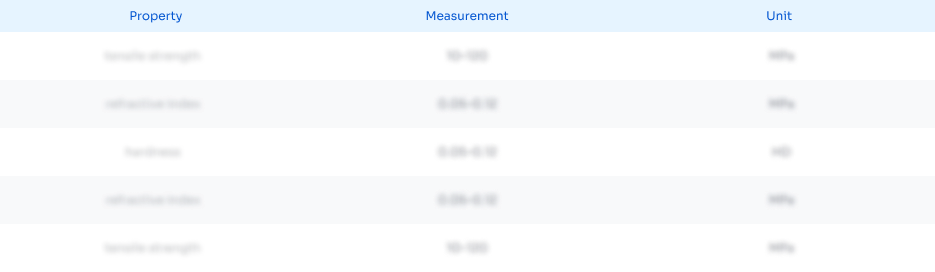
Abstract
Description
Claims
Application Information

- R&D
- Intellectual Property
- Life Sciences
- Materials
- Tech Scout
- Unparalleled Data Quality
- Higher Quality Content
- 60% Fewer Hallucinations
Browse by: Latest US Patents, China's latest patents, Technical Efficacy Thesaurus, Application Domain, Technology Topic, Popular Technical Reports.
© 2025 PatSnap. All rights reserved.Legal|Privacy policy|Modern Slavery Act Transparency Statement|Sitemap|About US| Contact US: help@patsnap.com