Method and device for manufacturing a single-layer abrasive wheel
A manufacturing method and grinding wheel technology, which are used in grinding devices, manufacturing tools, grinding/polishing equipment, etc., can solve the problem of loss of meaning in the control of the positional arrangement of single particles of abrasive grains, inconsistent benchmarks, and uneven control of the thickness of the brazing material layer. problems, to achieve the effect of improving preparation efficiency and process stability control, strong versatility, and high-quality brazing preparation
- Summary
- Abstract
- Description
- Claims
- Application Information
AI Technical Summary
Problems solved by technology
Method used
Image
Examples
Embodiment 1
[0041] like figure 1 and figure 2 As shown, a manufacturing device of a single-layer abrasive wheel includes a base 1, a data processing control assembly (not shown in the figure) and a rotating assembly 2 and a certain thickness assembly 3 arranged on the base 1 , a bonding agent coating assembly 4 and an abrasive particle sprinkle assembly 5 .
[0042]The rotating assembly 2 includes a rotating shaft 21, a driving motor 22 and a rotational motion control unit 23, the rotating shaft 21 drives the grinding wheel base 6 to rotate perpendicular to the horizontal plane under the drive of the driving motor 22, and the rotational motion control unit 23 is electrically connected to the driving motor 22 , to control the drive motor 22 to run at different speeds;
[0043] The thickness-fixing assembly 3 includes a certain thickness plate 31, a first uniaxial reciprocating mechanism 32, a displacement sensor 33, an angle sensor 34 and a runout data acquisition analysis and compensat...
PUM
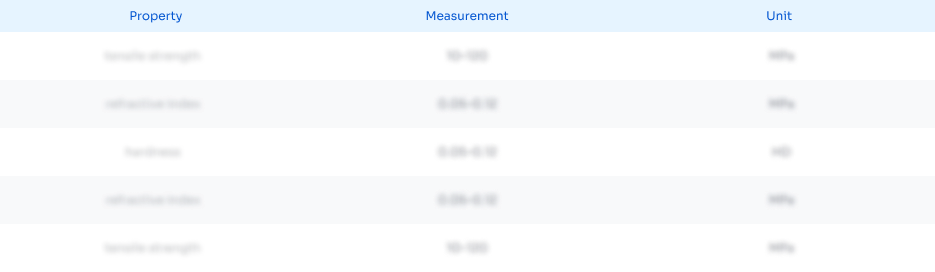
Abstract
Description
Claims
Application Information

- R&D
- Intellectual Property
- Life Sciences
- Materials
- Tech Scout
- Unparalleled Data Quality
- Higher Quality Content
- 60% Fewer Hallucinations
Browse by: Latest US Patents, China's latest patents, Technical Efficacy Thesaurus, Application Domain, Technology Topic, Popular Technical Reports.
© 2025 PatSnap. All rights reserved.Legal|Privacy policy|Modern Slavery Act Transparency Statement|Sitemap|About US| Contact US: help@patsnap.com