Wear-resistant transparent glaze and method for preparing glazed tile by utilizing same
A technology for transparent glazed and glazed tiles, which is applied in the field of architectural ceramics, can solve the problems of increased manufacturing cost, easy grinding, poor wear resistance, etc., and achieve the effects of low manufacturing cost, improved stain resistance, and good wear resistance
- Summary
- Abstract
- Description
- Claims
- Application Information
AI Technical Summary
Problems solved by technology
Method used
Image
Examples
Embodiment 1-10
[0020] With reference to the following table 1, the following table 1 is the formula table (wt%) of the wear-resistant transparent glaze provided by the present embodiment 1-5
[0021] Table 1
[0022]
[0023]
[0024] The above glazes are ball-milled and applied on the surface of conventional ceramic tiles. The ceramic tiles used are well-known bricks. The glaze is ball-milled to form a glaze slurry, and a glaze layer of about 1mm is formed on the surface of the tiles by pouring glaze, and then Put it into the kiln for firing, the firing temperature is 1200-1250°C, and the firing cycle is 2.5 hours. It needs to be explained here that, except for the glaze components, other technological processes mentioned above are the known methods for the production of architectural ceramics, and can be appropriately adjusted in different production lines. The frit used here is a transparent medium-temperature frit produced by common ceramics, and its applicable firing temperature ...
Embodiment 3
[0033] Select embodiment 3 to compare
[0034] In this example, spodumene was replaced by albite, and the results showed that the wear resistance of the glaze layer of the product was greatly improved, but the quality of the glaze layer was poor, with many pinhole defects, not stain resistant, and The flatness is poor.
Embodiment 6-8
[0036] In this series of examples, the rest of the components are the same as those in Example 4, except that the frit used is made by melting the raw materials of the following components at 1450-1550°C. The formula components are: 20-30% potassium feldspar, 3-6% wollastonite, 4-8% raw talc, 5-8% barium carbonate, 15-20% calcite, 18-22% quartz, 10-14 % alumina, 2-4% zinc oxide, 1-3% potassium carbonate, 1-2% strontium carbonate. specifically:
[0037] Embodiment 6-8 frit component is as follows table 2 (wt %)
[0038] Table 2
[0039]
[0040] Its wear resistance was tested to reach level 5, and the glaze surface is smoother, which can be polished until the thickness of the glaze layer is 0.3mm or less. This is because the frit, as a flux, also needs to have high wear resistance, so a relatively large amount of alumina is used in this component, and rare earth carbonate and zinc oxide are used as fluxes to make the frit It has high transparency and wear resistance, and...
PUM
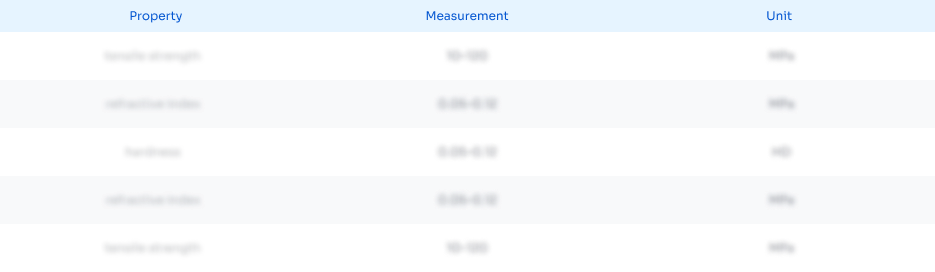
Abstract
Description
Claims
Application Information

- Generate Ideas
- Intellectual Property
- Life Sciences
- Materials
- Tech Scout
- Unparalleled Data Quality
- Higher Quality Content
- 60% Fewer Hallucinations
Browse by: Latest US Patents, China's latest patents, Technical Efficacy Thesaurus, Application Domain, Technology Topic, Popular Technical Reports.
© 2025 PatSnap. All rights reserved.Legal|Privacy policy|Modern Slavery Act Transparency Statement|Sitemap|About US| Contact US: help@patsnap.com