Methanol-to-gasoline combined technology
A methanol-to-gasoline and combined process technology is applied in the petroleum industry, the preparation of liquid hydrocarbon mixtures, and biological raw materials. rate, the effect of increasing the octane number
- Summary
- Abstract
- Description
- Claims
- Application Information
AI Technical Summary
Problems solved by technology
Method used
Image
Examples
Embodiment example
[0023] The embodiment of the scheme is described in combination with the process flow chart to further illustrate the present invention.
[0024]The methanol raw material 1 is pumped into the heating furnace 2, and part of the methanol vapor from the heating furnace 2 enters the dimethyl ether reactor 3. The dimethyl ether, water and unreacted methanol from the dimethyl ether reactor 3 enter the gasoline conversion reactors 4, 5 and 6, and the gasoline conversion reactors 4, 5 and 6 are produced by Wuhan Kelin Fine Chemical Co., Ltd. W221A type catalyst. After the product passes through the heat exchanger 7, it enters the oil-water separator 8 for oil-water separation, and the generated water 12 is separated.
[0025] The product after separating the generated water 12 from the oil-water separator 8 enters the deethanizer 9 . The separated dry gas 13 is divided into three parts: one part passes through the compressor 14 and then enters the heat exchanger 7 for preheating, an...
Embodiment example 1
[0029] In the dimethyl ether reactor 3, WD-1 catalyst produced by Wuhan Kelin Fine Chemical Co., Ltd. is used. The hot spot temperature is 260°C and the space velocity is 0.5h. -1 , The operating pressure is 3.0MPa.
[0030] Gasoline conversion reactors 4, 5 and 6 use W221A catalyst produced by Wuhan Kelin Fine Chemical Co., Ltd., the hot spot temperature is 420°C, and the operating pressure is 3.0MPa.
[0031] Part of the separated dry gas 13 passes through the compressor 14 and then enters the heat exchanger 7 for preheating, and then enters the gasoline conversion reactors 4, 5 and 6 with the dimethyl ether, water and unreacted methanol from the dimethyl ether reactor 3 , The dry gas circulation ratio entering the compressor 14 is 1:10.
[0032] The pressure at the top of the deethanizer 9 is 400kPa, and the temperature is 40°C. The pressure at the top of the debutanizer 10 is 1200 kPa, and the temperature is 60°C.
[0033] The liquefied gas 16 exiting the debutanizer 1...
Embodiment example 2
[0039] The WD-1 catalyst produced by Wuhan Kelin Fine Chemical Co., Ltd. is used in the dimethyl ether reactor 3, the hot spot temperature is 280°C, and the space velocity is 1.2h -1 , The operating pressure is 1.8MPa.
[0040] Gasoline conversion reactors 4, 5 and 6 use W221A catalyst produced by Wuhan Kelin Fine Chemical Co., Ltd., with a hot spot temperature of 330°C and an operating pressure of 1.8MPa.
[0041] Part of the separated dry gas 13 passes through the compressor 14 and then enters the heat exchanger 7 for preheating, and then enters the gasoline conversion reactors 4, 5 and 6 with the dimethyl ether, water and unreacted methanol from the dimethyl ether reactor 3 , The dry gas circulation ratio entering the compressor 14 is 15:1.
[0042] The pressure at the top of the deethanizer 9 is 800kPa, and the temperature is 55°C. The pressure at the top of the debutanizer 10 is 400 kPa, and the temperature is 40°C.
[0043] The liquefied gas 16 exiting the debutanize...
PUM
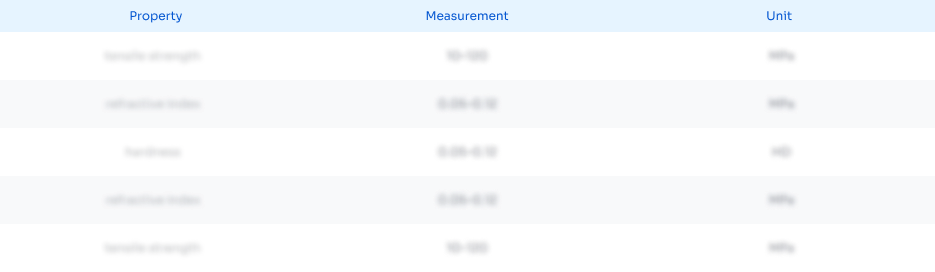
Abstract
Description
Claims
Application Information

- R&D
- Intellectual Property
- Life Sciences
- Materials
- Tech Scout
- Unparalleled Data Quality
- Higher Quality Content
- 60% Fewer Hallucinations
Browse by: Latest US Patents, China's latest patents, Technical Efficacy Thesaurus, Application Domain, Technology Topic, Popular Technical Reports.
© 2025 PatSnap. All rights reserved.Legal|Privacy policy|Modern Slavery Act Transparency Statement|Sitemap|About US| Contact US: help@patsnap.com