Regeneration repair method for tubular parts of die-casting machine
A repair method and die-casting machine technology, which is applied in the field of die-casting machine tubular parts repair, can solve the problems of increased cost of die-casting machine use, enlarged diameter of tubular fittings, and errors of die-casting machines, so as to achieve economical and environmentally friendly regenerative repairs, reduce effects, and reduce costs Effect
- Summary
- Abstract
- Description
- Claims
- Application Information
AI Technical Summary
Problems solved by technology
Method used
Examples
Embodiment Construction
[0012] The present invention will be described in detail below in conjunction with specific embodiments.
[0013] A method for regenerating and repairing a tubular fitting of a die-casting machine, comprising the following steps: a. Reaming: removing the worn part, and removing the worn part in the old tubular fitting by a lathe or a grinding tool; b. Welding: welding the inner diameter of the tubular fitting, Restore the original size of the hole, use inner diameter automatic welding equipment to repair the removed part of the tubular fitting after wear and tear; c, processing: deep processing with lathe and grinder to restore the tubular fitting to the original size or required according to the original drawing Dimensions; d. Surface treatment: Nitriding treatment is carried out on the surface of the tubular fittings after regeneration and repair. After the final welding is completed, the original size of the fittings is restored to complete the entire repair process.
[001...
PUM
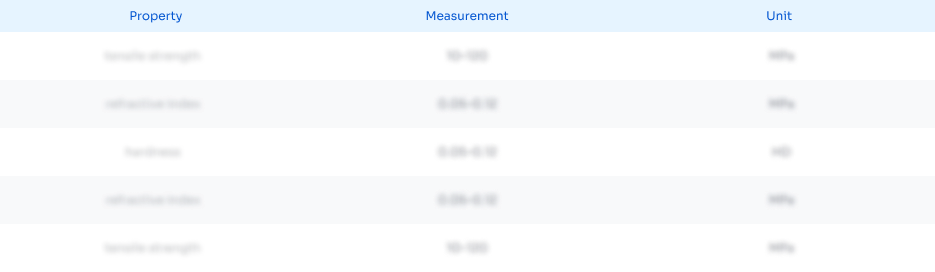
Abstract
Description
Claims
Application Information

- Generate Ideas
- Intellectual Property
- Life Sciences
- Materials
- Tech Scout
- Unparalleled Data Quality
- Higher Quality Content
- 60% Fewer Hallucinations
Browse by: Latest US Patents, China's latest patents, Technical Efficacy Thesaurus, Application Domain, Technology Topic, Popular Technical Reports.
© 2025 PatSnap. All rights reserved.Legal|Privacy policy|Modern Slavery Act Transparency Statement|Sitemap|About US| Contact US: help@patsnap.com