Polypropylene microcellular foam composite material and preparation method thereof
A composite material, polypropylene technology, applied in the field of polypropylene micro-foamed composite material and its preparation, can solve problems such as poor mechanical properties and complex production processes, achieve superior mechanical properties, enhance nucleation efficiency, and increase roughness Effect
- Summary
- Abstract
- Description
- Claims
- Application Information
AI Technical Summary
Problems solved by technology
Method used
Image
Examples
Embodiment 1
[0030] A polypropylene micro-foaming composite material is made of the following raw materials in parts by weight: 90 parts of polypropylene, 6 parts of carbon fiber and 4 parts of foaming masterbatch, and the foaming masterbatch is made of the following raw materials in parts by weight Composition: 60 parts of polyethylene, 25 parts of foaming agent, 3 parts of nucleating agent, 0.5 part of zinc oxide, 0.5 part of titanate coupling agent NDZ-201, 4 parts of PE wax and 0.7 part of zinc stearate. The foaming agent is calculated in parts by weight, including 65 parts of foaming agent TA-220; 35 parts of PP foaming multifunctional masterbatch and 5 parts of TA1000 foaming agent. The nucleating agent comprises 20 parts of talcum powder, 15 parts of calcium citrate and 65 parts of nano calcium carbonate in parts by weight.
[0031] Its preparation method comprises the following steps:
[0032] (1) Surface treatment of carbon fiber: the carbon fiber is surface-treated carbon fiber,...
Embodiment 2
[0038] A polypropylene micro-foaming composite material is made of the following raw materials in parts by weight: 85 parts of polypropylene, 5 parts of carbon fiber and 5 parts of foam masterbatch, and the foam masterbatch is made of the following raw materials in parts by weight Composition: 65 parts of polyethylene, 30 parts of foaming agent, 4 parts of nucleating agent, 1.5 parts of zinc oxide, 0.8 part of titanate coupling agent NDZ-201, 3 parts of PE wax and 0.5 part of zinc stearate. The foaming agent is calculated in parts by weight, including 60 parts of foaming agent TA-220; 40 parts of PP foaming multifunctional masterbatch and 3 parts of TA1000 foaming agent. The nucleating agent comprises 25 parts of talcum powder, 20 parts of calcium citrate and 60 parts of nano calcium carbonate in parts by weight.
[0039] Its preparation method comprises the following steps:
[0040] (1) Surface treatment of carbon fibers: the carbon fibers described are surface-treated carbo...
Embodiment 3
[0046] A polypropylene micro-foaming composite material is made of the following raw materials in parts by weight: 95 parts of polypropylene, 8 parts of carbon fiber and 4 parts of foaming masterbatch. The foaming masterbatch described in parts by weight is made of the following raw materials : 70 parts of polyethylene, 20 parts of foaming agent, 5 parts of nucleating agent, 1 part of zinc oxide, 1 part of titanate coupling agent NDZ-201, 5 parts of PE wax and 1 part of zinc stearate. The foaming agent is calculated in parts by weight, including 70 parts of foaming agent TA-220, 30 parts of PP foaming multifunctional masterbatch and 4 parts of TA1000 foaming agent. The nucleating agent comprises 30 parts of talcum powder, 10 parts of calcium citrate and 70 parts of nano calcium carbonate in parts by weight.
[0047] Its preparation method comprises the following steps:
[0048] (1) Surface treatment of carbon fibers: the carbon fibers described are surface-treated carbon fibe...
PUM
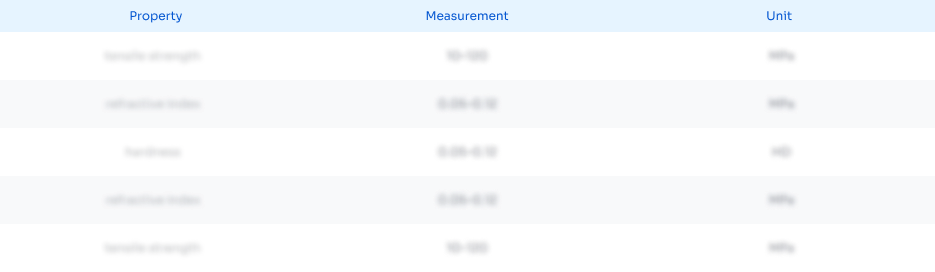
Abstract
Description
Claims
Application Information

- R&D Engineer
- R&D Manager
- IP Professional
- Industry Leading Data Capabilities
- Powerful AI technology
- Patent DNA Extraction
Browse by: Latest US Patents, China's latest patents, Technical Efficacy Thesaurus, Application Domain, Technology Topic, Popular Technical Reports.
© 2024 PatSnap. All rights reserved.Legal|Privacy policy|Modern Slavery Act Transparency Statement|Sitemap|About US| Contact US: help@patsnap.com