Thin-wall component recombining and restoring method based on pulse welding and laser augmented material restoring
A laser additive and pulse welding technology, which is applied in the repair and remanufacturing of damaged parts, can solve problems such as limiting the scope of application of laser additive repair technology, increasing repair auxiliary time and cost, and increasing the complexity of the repair process. Achieve the effects of improving repair efficiency, small deformation, and strong bridging ability
- Summary
- Abstract
- Description
- Claims
- Application Information
AI Technical Summary
Problems solved by technology
Method used
Image
Examples
Embodiment Construction
[0022] As shown in Figure 1-6, the composite repair method of thin-walled parts based on pulse welding and laser additive repair includes damage crack 1, damage envelope 2, carbide rotary file 3, and through-groove after grinding 4 , Groove 5, precision pulse welding machine 6, bridging welding restoration, welding torch 8, laser 9, optical path system 10, coaxial powder feeding head 11, workbench 12, blind groove 13, restoration 14. The repair method is as follows: 1. If figure 1 Shown is part 1 with penetrating damage such as cracks. Before the repair, the coloring inspection method is used to determine the distribution and direction of penetrating damage such as cracks, and the contour minimum envelope method is used to regularize the polished damage area 2, such as figure 2 2. Carbide rotary file is used for grinding treatment to form a relatively regular through-groove, while grinding and coloring inspection, until the penetrating damage such as cracks is completely rem...
PUM
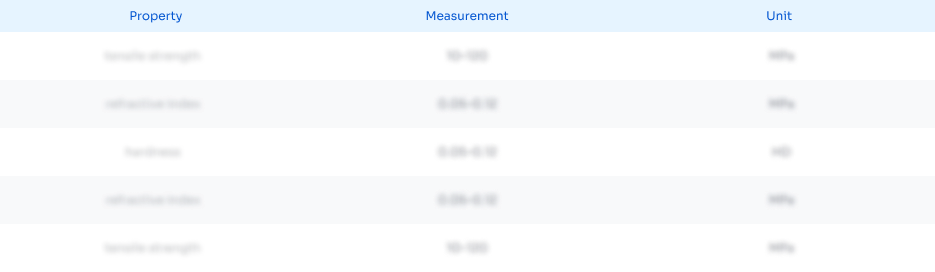
Abstract
Description
Claims
Application Information

- R&D
- Intellectual Property
- Life Sciences
- Materials
- Tech Scout
- Unparalleled Data Quality
- Higher Quality Content
- 60% Fewer Hallucinations
Browse by: Latest US Patents, China's latest patents, Technical Efficacy Thesaurus, Application Domain, Technology Topic, Popular Technical Reports.
© 2025 PatSnap. All rights reserved.Legal|Privacy policy|Modern Slavery Act Transparency Statement|Sitemap|About US| Contact US: help@patsnap.com