Tail wing pouring system and tail wing manufacturing method for aluminum alloy underwater launching tube
An underwater launch and pouring system technology, applied in the field of pressure-resistant sealed container manufacturing, can solve the problems of low material utilization, high cost of forged castings, and difficult control of deformation, so as to improve internal quality and compactness, and ensure shape and size Good effect of precision, stability and shock resistance
- Summary
- Abstract
- Description
- Claims
- Application Information
AI Technical Summary
Problems solved by technology
Method used
Image
Examples
Embodiment Construction
[0030] Below in conjunction with accompanying drawing and specific embodiment the present invention is described in further detail:
[0031] like Figure 1~4 The aluminum alloy underwater launching tube empennage pouring system includes a runner 7, a sprue 8, and a plurality of vertical tubes 6 corresponding to the wings 1 in the underwater launching tube empennage casting, and the runner 7 and the sprue 8 are all located at the bottom of the vertical tube 6, the sprue 8 communicates with the runner 7, the runner 7 communicates with the bottom of each vertical tube 6, and the empennage castings of the underwater launching tube are located at all Inside the cylindrical area surrounded by the vertical tube 6, there is a gap 5 between the empennage casting of the underwater launching tube and the outer side wall of each vertical tube 6, and the top of each vertical tube 6 communicates with the corresponding gap 5, and the water The inner cavity of the lower launching tube empenn...
PUM
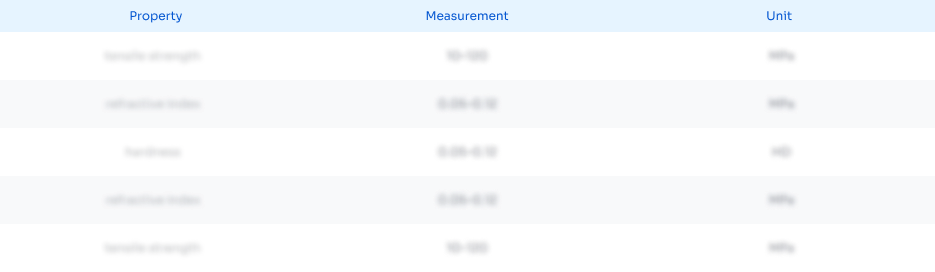
Abstract
Description
Claims
Application Information

- Generate Ideas
- Intellectual Property
- Life Sciences
- Materials
- Tech Scout
- Unparalleled Data Quality
- Higher Quality Content
- 60% Fewer Hallucinations
Browse by: Latest US Patents, China's latest patents, Technical Efficacy Thesaurus, Application Domain, Technology Topic, Popular Technical Reports.
© 2025 PatSnap. All rights reserved.Legal|Privacy policy|Modern Slavery Act Transparency Statement|Sitemap|About US| Contact US: help@patsnap.com