Ceramic metal anti-corrosion pipe and forming technology
A technology of ceramic metal and forming process, which is applied in pipeline anticorrosion/rust protection, damage protection, pipeline protection, etc. It can solve the problems of no improvement in product quality and stability, low degree of automation of centrifuges, and manual operation. Good firmness, high mechanical performance and long service life
- Summary
- Abstract
- Description
- Claims
- Application Information
AI Technical Summary
Problems solved by technology
Method used
Examples
Embodiment 1
[0018] Example 1: put the tubing into a centrifugal device, dry iron powder, elemental aluminum powder and silicon powder at a temperature of 170 degrees Celsius, and put 10666g of iron powder, 4800g of elemental aluminum powder and 533g of silicon powder into the mixture after drying Mixing in the machine, the mixing time is 0.45 hours, during the mixing process, iron powder and elemental aluminum powder are mixed according to 2Al+Fe 2 o 3 =Al 2 o 3 +2Fe+836Kj / mol The melt product formed by the reaction is stable a-Al2O3 and Fe, and a large amount of heat is released at the same time, which ensures the continuous progress of the reaction;
[0019] Put the melt product into the oil pipe, turn on the centrifugal equipment, the centrifugal equipment drives the oil pipe to rotate at high speed, and the speed of the oil pipe is controlled at 2150r / min to 2250r / min. After the tubing rotates at a high speed, the melt product is rapidly separated according to the specific gravity ...
Embodiment 2
[0020] Example 2: put the tubing into a centrifugal device, dry iron powder, elemental aluminum powder and silicon powder at a temperature of 170 degrees Celsius, and put 10667g of iron powder, 4267g of elemental aluminum powder and 1066g of silicon powder into the mixture after drying Mixing in the machine, the mixing time is 0.55 hours, during the mixing process, iron powder and elemental aluminum powder are mixed according to 2Al+Fe 2 o 3 =Al 2 o 3 +2Fe+836Kj / mol The melt product formed by the reaction is stable a-Al2O3 and Fe, and a large amount of heat is released at the same time, which ensures the continuous progress of the reaction;
[0021] Put the melt product into the oil pipe, turn on the centrifugal equipment, the centrifugal equipment drives the oil pipe to rotate at high speed, and the speed of the oil pipe is controlled at 2150r / min to 2250r / min. After the tubing rotates at a high speed, the melt product is rapidly separated according to the specific gravity...
PUM
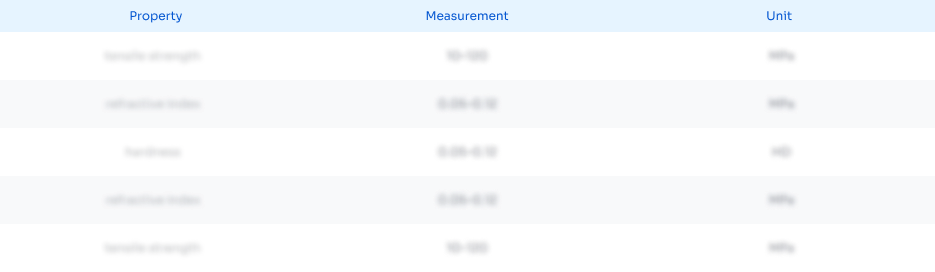
Abstract
Description
Claims
Application Information

- R&D Engineer
- R&D Manager
- IP Professional
- Industry Leading Data Capabilities
- Powerful AI technology
- Patent DNA Extraction
Browse by: Latest US Patents, China's latest patents, Technical Efficacy Thesaurus, Application Domain, Technology Topic, Popular Technical Reports.
© 2024 PatSnap. All rights reserved.Legal|Privacy policy|Modern Slavery Act Transparency Statement|Sitemap|About US| Contact US: help@patsnap.com