Porous silicon-carbon composite material and preparation method and application thereof
A carbon composite material and composite material technology, applied in the field of porous silicon-carbon composite material and its preparation, can solve the problems of difficult industrialization, high equipment requirements, high cost, etc., achieve short transmission distance and alleviate volume expansion effect , the effect of improving conductivity
- Summary
- Abstract
- Description
- Claims
- Application Information
AI Technical Summary
Problems solved by technology
Method used
Image
Examples
Embodiment 1
[0030] 1) Heat-treat magnesium silicide at 700°C for 20 hours, and pass excess CO 2 80% CO by volume 2 / Ar mixed gas as the reaction gas.
[0031] 2) The product obtained in step 1) was treated for 10 hours in a certain concentration of hydrochloric acid solution, wherein the concentration of hydrochloric acid was 0.5 mol / liter, after the acid treatment, it was washed 5 times with deionized water, then centrifuged, and finally vacuum-dried.
[0032] The relevant characterization results of the porous silicon-carbon composite material prepared in this example are as follows figure 1 shown. It can be seen from the figure that the product of this example is a porous structure with a large number of uniformly distributed nanoscale pores, the mass fraction of carbon is about 40%, and it is uniformly coated on the surface of silicon in the form of an amorphous carbon film, forming a porous structure with a core. -Silicon-carbon composite material with shell structure characterist...
Embodiment 2
[0036] The preparation process is exactly the same as in Example 1, the difference is only that CO 2 / Ar mixture, CO 2 The volume fraction is 60%. The morphology of the prepared porous silicon-carbon composite material is similar to that of Example 1, but the mass fraction of carbon is about 45%.
Embodiment 3
[0038] 1) Heat-treat magnesium silicide at 800°C for 15 hours, and pass excess CO 2 50% CO by volume 2 / Ar mixed gas as the reaction gas.
[0039] 2) The product obtained in step 1) was treated for 5 hours in a certain concentration of hydrochloric acid solution, wherein the concentration of hydrochloric acid was 2.0 mol / liter, after the acid treatment, it was washed 7 times with deionized water, then centrifuged, and finally vacuum-dried.
[0040] The morphology of the porous silicon-carbon composite material prepared in this example is similar to that of Example 1, but the mass fraction of carbon is about 46%.
[0041] The porous silicon-carbon composite material prepared in this example was made into a button battery for performance testing, and the cycle specific capacity and Coulombic efficiency were compared with the porous silicon-carbon composite material prepared in the comparative example, as shown in image 3 shown. It can be seen from the figure that after 50 cy...
PUM
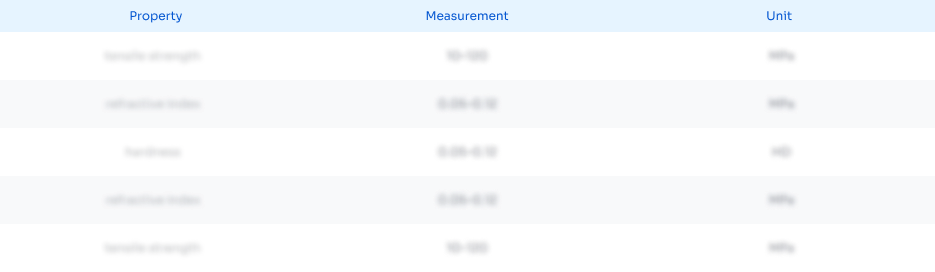
Abstract
Description
Claims
Application Information

- Generate Ideas
- Intellectual Property
- Life Sciences
- Materials
- Tech Scout
- Unparalleled Data Quality
- Higher Quality Content
- 60% Fewer Hallucinations
Browse by: Latest US Patents, China's latest patents, Technical Efficacy Thesaurus, Application Domain, Technology Topic, Popular Technical Reports.
© 2025 PatSnap. All rights reserved.Legal|Privacy policy|Modern Slavery Act Transparency Statement|Sitemap|About US| Contact US: help@patsnap.com