Smelting method for ultra-low carbon steel
A smelting method and technology for ultra-low carbon steel, applied in the field of iron and steel smelting, can solve the problem of high oxide inclusions, and achieve the effects of improving the cleanliness of molten steel, improving pourability, and reducing oxidizability
- Summary
- Abstract
- Description
- Claims
- Application Information
AI Technical Summary
Problems solved by technology
Method used
Image
Examples
Embodiment 1
[0032] The embodiment of the present application provides a method for smelting ultra-low carbon steel, including:
[0033] Step S1: Smelting molten iron through a converter, and adding high-calcium-aluminum slag balls according to the oxygen content at the end of the converter to reduce the TFe content in the top slag when tapping the converter, thereby obtaining molten steel;
[0034] Step S2: vacuum refining the molten steel through RH, and evenly sprinkle high-calcium aluminum slag balls on the slag surface at the end of RH breaking to further reduce the TFe content in the slag, thereby obtaining molten steel with high cleanliness;
[0035] Step S3: Continuous casting the molten steel with high cleanliness to obtain a finished product.
[0036] Wherein, in step S1, the molten iron is smelted by a converter to obtain molten steel. When the converter is tapping, adding high-calcium aluminum slag balls according to the oxygen content at the end of the converter to reduce the ...
Embodiment 2
[0062] In the examples of this application, the initial C content of molten iron is 4.48%, the P content is 0.085%, the converter tapping temperature is controlled at 1682°C, the final carbon content is 0.039%, the P content is 0.0070%, and the final oxygen content is 706ppm. The steel time is 466s, 98.92kg of bauxite is added, 508.1kg of small lime is added, and 346.1kg of high-calcium aluminum slag balls are added according to the calculation of oxygen content. The TFe of the slag is 15.68%, the TFe of the slag at the end of RH is 4.95%, and the TFe of the slag before the end of RH is 3.73%. After adopting the above dynamic two-step slag reforming process, the final slag TFe of converter tapping is reduced from 15.68% to 3.73% of the TFe of the slag before the RH ends. Package T.[O] can be controlled at 20×10 -6 Therefore, the TFe content in the ultra-low carbon steel slag is significantly reduced, which plays a role in reducing the oxidation of slag and improving the clean...
Embodiment 3
[0064] In the examples of this application, the initial C content of smelted molten iron is 4.04%, the P content is 0.076%, the converter tapping temperature is controlled at 1703°C, the final carbon content is 0.024%, the P content is 0.0097%, and the final oxygen content is 603ppm. The steel time is 510s, 100.03kg of bauxite is added, 488.9kg of small lime is added, and 330.4kg of high-calcium aluminum slag balls are added according to the calculation of oxygen content. The slag TFe is 16.21%, the slag TFe after RH is 3.4%, and the slag TFe before RH is 2.15%. After adopting the above dynamic two-step slag reforming process, the final slag TFe of converter tapping is reduced from 16.21% to 2.15% of the TFe of the slag before the end of RH. The T.[O] content is 0.0022%, so the TFe content in the ultra-low carbon steel slag is significantly reduced, which can reduce the oxidation of slag and improve the cleanliness of molten steel.
PUM
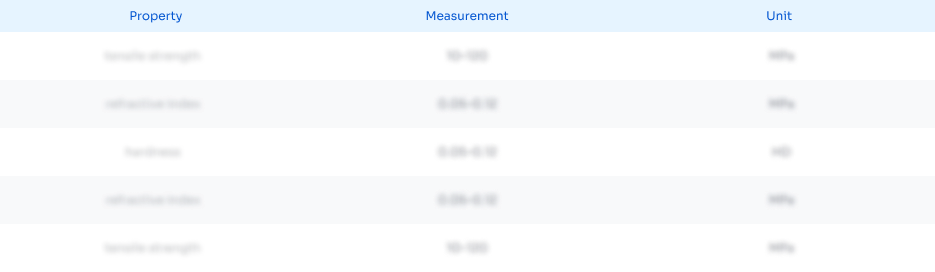
Abstract
Description
Claims
Application Information

- Generate Ideas
- Intellectual Property
- Life Sciences
- Materials
- Tech Scout
- Unparalleled Data Quality
- Higher Quality Content
- 60% Fewer Hallucinations
Browse by: Latest US Patents, China's latest patents, Technical Efficacy Thesaurus, Application Domain, Technology Topic, Popular Technical Reports.
© 2025 PatSnap. All rights reserved.Legal|Privacy policy|Modern Slavery Act Transparency Statement|Sitemap|About US| Contact US: help@patsnap.com