Semi-steel smelting steelmaking method with constant pressure and constant gun
A technology for steel smelting and tons of steel, which is applied to the field of semi-steel smelting with constant pressure and constant guns, can solve problems such as increasing costs, and achieve the effects of stable process, reduced TFe content, and reduced chances of re-drying and splashing.
- Summary
- Abstract
- Description
- Claims
- Application Information
AI Technical Summary
Problems solved by technology
Method used
Examples
Embodiment 1
[0040] A 120t converter in a factory uses semi-steel steelmaking, and the working pressure of the oxygen lance is constant at 0.90MPa. After the smelting of the previous furnace, 6kg / ton of high-magnesia lime and 10kg / ton of active lime are added to the furnace, and the furnace is shaken back and forth to mix well. Then add semi-steel and start blowing oxygen. The total amount of composite slagging agent is 15kg / ton of steel. When the progress of oxygen blowing is 0%, 90% of the remaining active lime, high magnesium lime and the total amount of composite slagging agent (13.5kg / ton of steel) are added to the furnace at one time. At the same time, quantitatively add corundum slag 1kg / ton of steel (corundum slag composition is Al 2 o 3 : 60%, CaO: 10%, MgO: 15%, V 2 o 5: 4%, the rest are impurities, the particle size is 10-50mm), when the oxygen blowing progress is 45%, 0.75kg / ton of corundum slag is added quantitatively, and 5% of the total amount of composite slagging agent ...
Embodiment 2
[0042] A factory’s 120t converter adopts semi-steel steelmaking, and the working pressure of the oxygen lance is constant at 0.90MPa. After the smelting of the previous furnace, 8kg / ton of high-magnesia lime and 8kg / ton of active lime are added to the furnace, and the furnace is shaken back and forth to mix well. Then add semi-steel and start blowing oxygen. The total amount of composite slagging agent is 18kg / ton of steel, and when the progress of oxygen blowing is 15%, 90% of the remaining active lime, high magnesium lime and the total amount of composite slagging agent (16.2kg / ton of steel) are added to the furnace at one time At the same time, quantitatively add corundum slag 1kg / ton of steel (corundum slag composition is Al 2 o 3 : 65%, CaO: 8%, MgO: 12%, V 2 o 5 : 3%, the rest are impurities, the particle size is 10-50mm), when the oxygen blowing progress is 48%, add corundum slag 0.75kg / ton of steel quantitatively, and add 5% of the total amount of composite slagging...
Embodiment 3
[0044] A 120t converter in a factory uses semi-steel steelmaking, and the working pressure of the oxygen lance is constant at 0.90MPa. After the smelting of the previous furnace, 10kg / ton of high-magnesia lime and 10kg / ton of active lime are added to the furnace, and the furnace is shaken back and forth to mix well. Then add semi-steel and start blowing oxygen. The total amount of composite slagging agent is 16kg / ton of steel. When the progress of oxygen blowing is 30%, 90% of the remaining active lime, high magnesium lime and the total amount of composite slagging agent (14.4kg / ton of steel) are added to the furnace at one time. At the same time, quantitatively add corundum slag 1kg / ton of steel (corundum slag composition is Al 2 o 3 : 70%, CaO: 5%, MgO: 10%, V 2 o 5 : 1%, the rest are impurities, the particle size is 10-50mm), when the progress of oxygen blowing is 50%, 0.75kg / ton of steel is added quantitatively, and 5% of the total amount of composite slagging agent (0....
PUM
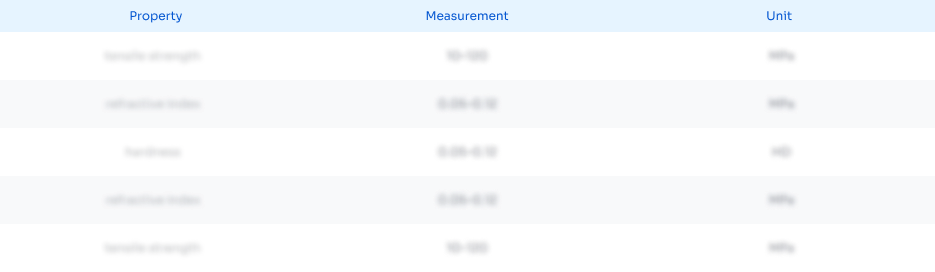
Abstract
Description
Claims
Application Information

- R&D
- Intellectual Property
- Life Sciences
- Materials
- Tech Scout
- Unparalleled Data Quality
- Higher Quality Content
- 60% Fewer Hallucinations
Browse by: Latest US Patents, China's latest patents, Technical Efficacy Thesaurus, Application Domain, Technology Topic, Popular Technical Reports.
© 2025 PatSnap. All rights reserved.Legal|Privacy policy|Modern Slavery Act Transparency Statement|Sitemap|About US| Contact US: help@patsnap.com