Method for preparing halogenated polymer
A halogenated polymer and polymer technology, applied in the field of halogenated polymer preparation, can solve the problems of affecting the performance of halogenated polymers, unable to remove initiators, unable to neutralize hydrogen halide, etc., and achieve simple and feasible process conditions and steps, The effect of promoting neutralization reaction and promoting decomposition
- Summary
- Abstract
- Description
- Claims
- Application Information
AI Technical Summary
Problems solved by technology
Method used
Examples
Embodiment 1
[0027](1) Fix the 1000mL glass three-necked flask equipped with a strong constant speed stirring device in an ultrasonic cleaner, add 40g of prepared isobutylene / p-methylstyrene copolymer in the three-necked flask, and then add n-hexane to prepare a concentration of 10wt % glue. Add 1.5 mol% liquid bromine, mix and stir for 1 minute, add 0.08 g of azobisisoheptanonitrile, and carry out bromination at 56°C. After 12 minutes, the red color of the glue disappeared, and the bromination reaction was completed. Quickly adopt glass sampling tube to carry out sampling, to wait for the hydrogen bromide content in the glue solution to be analyzed by nuclear magnetic resonance spectroscopy, and adopt the infrared spectrometer to measure the content of the initiator in the glue solution.
[0028] Immediately add 60mL of 1wt% NaOH aqueous solution to the three-necked bottle, turn on the switch of the ultrasonic cleaner (frequency 60KHz), adjust the heating temperature adjustment knob of t...
Embodiment 2
[0033] (1) Fix the 1000mL glass three-necked flask equipped with a strong constant speed stirring device in an ultrasonic cleaner, add 40g of prepared isobutylene / p-methylstyrene copolymer in the three-necked flask, and then add n-hexane to prepare a concentration of 10wt % glue. Add 1.7 mol% liquid bromine, mix and stir for 1 minute, add 0.10 g of azobisisoheptanonitrile, and carry out bromination at 56°C. After 12 minutes, the red color of the glue disappeared, and the bromination reaction was completed. Quickly adopt glass sampling tube to carry out sampling, to wait for the hydrogen bromide content in the glue solution to be analyzed by nuclear magnetic resonance spectroscopy, and adopt the infrared spectrometer to measure the content of the initiator in the glue solution.
[0034] Immediately add 40mL of 1wt% Na to the three-neck flask 2 CO 3 For aqueous solution, turn on the switch of the ultrasonic cleaner (frequency 80KHz), adjust the heating temperature adjustment ...
Embodiment 3
[0039] (1) A 1000mL glass three-necked flask equipped with a powerful constant-speed stirring device is fixed in an ultrasonic cleaner, and 40 g of the prepared isobutylene / p-methylstyrene copolymer is added to the three-necked flask, and then cyclohexane is added to form a concentration of 10wt% glue solution. Add 2.0 mol% liquid bromine, mix and stir for 1 minute, add 0.12 g of azobisisoheptanonitrile, and brominate at 56°C. After 12 minutes, the red color of the glue disappeared, and the bromination reaction was completed. Quickly adopt glass sampling tube to carry out sampling, to wait for the hydrogen bromide content in the glue solution to be analyzed by nuclear magnetic resonance spectroscopy, and adopt the infrared spectrometer to measure the content of the initiator in the glue solution.
[0040] Immediately add 80mL of 1wt% KOH aqueous solution to the three-necked flask, turn on the switch of the ultrasonic cleaner (frequency 120KHz), and ultrasonically disperse for...
PUM
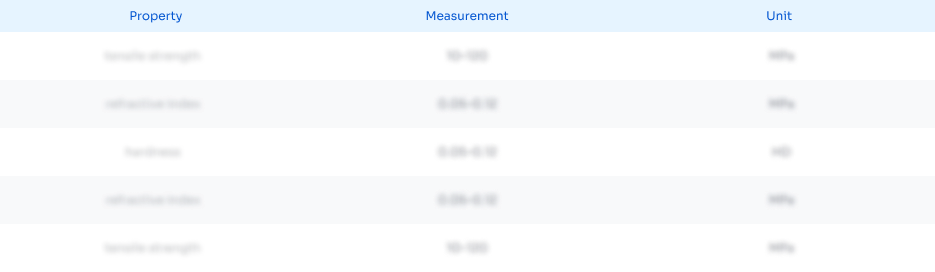
Abstract
Description
Claims
Application Information

- R&D
- Intellectual Property
- Life Sciences
- Materials
- Tech Scout
- Unparalleled Data Quality
- Higher Quality Content
- 60% Fewer Hallucinations
Browse by: Latest US Patents, China's latest patents, Technical Efficacy Thesaurus, Application Domain, Technology Topic, Popular Technical Reports.
© 2025 PatSnap. All rights reserved.Legal|Privacy policy|Modern Slavery Act Transparency Statement|Sitemap|About US| Contact US: help@patsnap.com