Preparation method of clay and modified butadiene styrene rubber nanocomposite for inner liner of tire
A nano-composite material, styrene-butadiene rubber technology, applied in special tires, tire parts, transportation and packaging, etc., can solve the problems of unimproved interfacial strength, increased clay lamella spacing, poor compatibility, etc., to improve Dispersion, improve airtight performance, low cost effect
- Summary
- Abstract
- Description
- Claims
- Application Information
AI Technical Summary
Problems solved by technology
Method used
Image
Examples
Embodiment 1
[0030] First, add deionized water into the reaction kettle, stir evenly, start stirring and heat up to 50°C, then add 1g of potassium persulfate, 290g of styrene, 10g of 2-vinylpyridine, add 700g of butadiene after vacuuming, and the whole polymerization The process controls the polymerization temperature at 50°C±2°C. When the conversion rate reaches 100%, the polymerization is terminated, and the material is discharged at room temperature to obtain the product. The appearance of the product is milky white and translucent, and its solid content is about 40% (mass percentage, the same below).
[0031] Then commercially available sodium-based bentonite is stirred in deionized water, left standstill after mixing uniformly, and the final solid content is controlled at 0.1% (mass percentage, the same below), and the clay aqueous suspension 100g is mixed with the above-mentioned modified styrene-butadiene latex 250g Stir and mix at room temperature, and then pour it into 0.5% (mass ...
Embodiment 2
[0033] First, add deionized water into the reaction kettle, stir evenly, start stirring and heat up to 55°C, then add 2g of potassium persulfate, 260g of styrene, 20g of 2-vinylpyridine, add 720g of butadiene after vacuuming, and the whole polymerization The process controls the polymerization temperature at 55°C±2°C. When the conversion rate reaches 90%, the polymerization is terminated, and the material is discharged at room temperature to obtain the product. The appearance of the product is milky white and translucent, and its solid content is about 36%.
[0034]Then commercially available sodium-based bentonite was stirred in deionized water, mixed uniformly and left to stand, the final solid content was controlled at 1%, the clay aqueous suspension 100g and the above-mentioned modified styrene-butadiene latex 278g were stirred and mixed at room temperature, Then pour it into 1% hydrochloric acid solution for flocculation. The flocculation product is washed clean, and the...
Embodiment 3
[0036] First, add deionized water into the reaction kettle, stir evenly, start stirring and raise the temperature to 60°C, then add 5g of ammonium persulfate, 240g of styrene, 20g of 2-vinylpyridine, add 740g of butadiene after vacuuming, and the whole polymerization The process controls the polymerization temperature at 60°C±2°C. When the conversion rate reaches 85%, the polymerization is terminated, and the material is discharged at room temperature to obtain the product. The appearance of the product is milky white and translucent, and its solid content is about 34%.
[0037] Then commercially available sodium-based bentonite was stirred in deionized water, mixed uniformly and left to stand, the final solid content was controlled at 2%, and 250 g of the clay aqueous suspension was stirred and mixed with the above-mentioned modified styrene-butadiene latex 294 g at room temperature, Then pour it into 1.5% sodium chloride solution for flocculation. The flocculation product i...
PUM
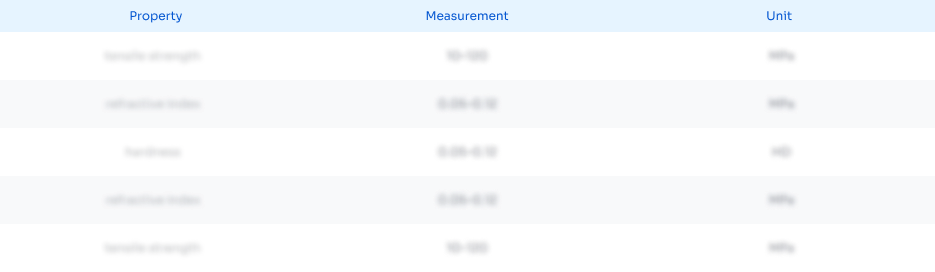
Abstract
Description
Claims
Application Information

- R&D Engineer
- R&D Manager
- IP Professional
- Industry Leading Data Capabilities
- Powerful AI technology
- Patent DNA Extraction
Browse by: Latest US Patents, China's latest patents, Technical Efficacy Thesaurus, Application Domain, Technology Topic, Popular Technical Reports.
© 2024 PatSnap. All rights reserved.Legal|Privacy policy|Modern Slavery Act Transparency Statement|Sitemap|About US| Contact US: help@patsnap.com