Method for reducing dielectric loss of niobate-based glass ceramic high voltage capacitor device
A technology of high-voltage capacitors and glass ceramics, which is applied in the field of reducing the dielectric loss of niobate-based glass ceramic high-voltage capacitor devices, can solve the problems of unsatisfactory performance requirements, large dielectric loss, and temperature rise, so as to ensure uniform nucleation and Effects of growth, reduction of dielectric loss, and improvement of stability
- Summary
- Abstract
- Description
- Claims
- Application Information
AI Technical Summary
Problems solved by technology
Method used
Examples
Embodiment 1
[0024] Choose PbO, SrCO with a purity greater than 99.5% 3 , Nb 2 o 5 、Na 2 CO 3 , SiO 2 and Al 2 o 3 As raw material, according to 5PbO-9SrCO 3 -30Nb 2 o 5 -15Na 2 CO 3 -24SiO2 2 -0.024Al 2 o 3 (molar ratio) was batched, and then mixed for 4 hours using a tumble mixer. Then the homogeneously mixed raw materials were put into a platinum crucible and melted at a high temperature of 1370°C for 2 hours. Then quickly pour the evenly melted molten glass into a metal mold preheated to 550°C in advance. After forming, put it into an annealing furnace for stress relief annealing. After 6 hours of heat preservation, turn off the annealing furnace and cool with the furnace to prepare a uniform glass. Transparent glass sheet.
[0025]The prepared glass sheet is subjected to controllable crystallization heat treatment, and the treatment process is as follows: firstly, the temperature is kept at 600°C for 3 hours to promote the uniform nucleation of the main ceramic phase, ...
Embodiment 2
[0028] Choose PbO, SrCO with a purity greater than 99.5% 3 , Nb 2 o 5 、Na 2 CO 3 , SiO 2 and Al 2 o 3 As raw material, according to 6PbO-10SrCO 3 -32Nb 2 o 5 -16Na 2 CO 3 -30SiO 2 -1.2Al 2 o 3 (molar ratio) was batched, and then mixed for 4 hours using a tumble mixer. Then the homogeneously mixed raw materials were put into a platinum crucible and melted at a high temperature of 1370°C for 2 hours. Then quickly pour the evenly melted molten glass into a metal mold preheated to 550°C in advance. After forming, put it into an annealing furnace for stress relief annealing. After 6 hours of heat preservation, turn off the annealing furnace and cool with the furnace to prepare a uniform glass. Transparent glass sheet.
[0029] The prepared glass sheet is subjected to controllable crystallization heat treatment, and the treatment process is as follows: firstly, the temperature is kept at 600°C for 3 hours to promote the uniform nucleation of the main ceramic phase, a...
Embodiment 3
[0032] Choose PbO, SrCO with a purity greater than 99.5% 3 , Nb 2 o 5 、Na 2 CO 3 , SiO 2 and Al 2 o 3 As raw material, according to 5PbO-10SrCO 3 -33Nb 2 o 5 -18Na 2 CO 3 -35SiO 2 -0.21Al 2 o 3 (molar ratio) was batched, and then mixed for 4 hours using a tumble mixer. Then the homogeneously mixed raw materials were put into a platinum crucible and melted at a high temperature of 1370°C for 2 hours. Then quickly pour the evenly melted molten glass into a metal mold preheated to 550°C in advance. After forming, put it into an annealing furnace for stress relief annealing. After 6 hours of heat preservation, turn off the annealing furnace and cool with the furnace to prepare a uniform glass. Transparent glass sheet.
[0033] The prepared glass sheet is subjected to controllable crystallization heat treatment, and the treatment process is as follows: firstly, the temperature is kept at 600°C for 3 hours to promote the uniform nucleation of the main ceramic phase, ...
PUM
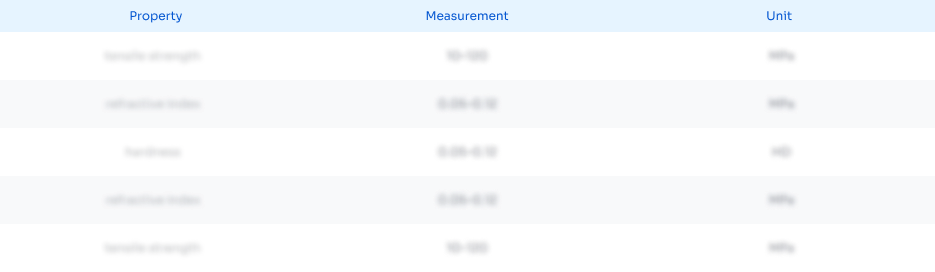
Abstract
Description
Claims
Application Information

- Generate Ideas
- Intellectual Property
- Life Sciences
- Materials
- Tech Scout
- Unparalleled Data Quality
- Higher Quality Content
- 60% Fewer Hallucinations
Browse by: Latest US Patents, China's latest patents, Technical Efficacy Thesaurus, Application Domain, Technology Topic, Popular Technical Reports.
© 2025 PatSnap. All rights reserved.Legal|Privacy policy|Modern Slavery Act Transparency Statement|Sitemap|About US| Contact US: help@patsnap.com