A kind of cashmere grinding sand disc and its production process
A production process and grinding sand technology, applied in abrasives, grinding devices, manufacturing tools, etc., can solve problems such as high cost, low efficiency, complex production process, etc., and achieve high grinding efficiency and ensure safety.
- Summary
- Abstract
- Description
- Claims
- Application Information
AI Technical Summary
Problems solved by technology
Method used
Image
Examples
Embodiment 1
[0044] A kind of cashmere grinding disc provided in this embodiment has a structure such as Figure 1-3 As shown, it includes a flannelette layer 1 and an abrasive cloth layer. The abrasive cloth layer includes a substrate layer and an abrasive layer. The center of the substrate layer is provided with an installation hole 2. The surface of the substrate layer is evenly distributed with spiral grooves 3. Inside the spiral groove 3 No binder, no abrasive, the substrate layer includes a first substrate layer 4 and a second substrate layer 5, the abrasive layer includes a first abrasive layer 6 and a second abrasive layer 7, and the upper surface of the first substrate layer 4 passes through The binder is bonded with the first abrasive layer 6, the lower surface of the first substrate layer 4 is bonded with the second abrasive layer 7 by the binder, and the second abrasive layer 7 is bonded away from the first substrate layer 4 by bonding. The binder is bonded with a second base m...
Embodiment 2
[0065] A kind of cashmere grinding disc provided in this embodiment has a structure such as figure 1 and 2 As shown, it comprises flannelette layer 1 and emery cloth layer, and emery cloth layer comprises base material layer and abrasive material layer, and base material layer center position is provided with mounting hole 2, is evenly distributed with spiral groove 3 on the surface of base material layer, and inside spiral groove 3 No binder, no abrasive, the substrate layer includes a first substrate layer 4 and a second substrate layer 5, the abrasive layer includes a first abrasive layer 6 and a second abrasive layer 7, and the upper surface of the first substrate layer 4 passes through The binder is bonded with the first abrasive layer 6, the lower surface of the first substrate layer 4 is bonded with the second abrasive layer 7 by the binder, and the second abrasive layer 7 is bonded away from the first substrate layer 4 by bonding. The binder is bonded with a second ba...
Embodiment 3
[0086] A kind of cashmere grinding disc provided in this embodiment has a structure such as figure 1 and 2 As shown, it comprises flannelette layer 1 and emery cloth layer, and emery cloth layer comprises base material layer and abrasive material layer, and base material layer center position is provided with mounting hole 2, is evenly distributed with spiral groove 3 on the surface of base material layer, and inside spiral groove 3 No binder, no abrasive, the substrate layer includes a first substrate layer 4 and a second substrate layer 5, the abrasive layer includes a first abrasive layer 6 and a second abrasive layer 7, and the upper surface of the first substrate layer 4 passes through The binder is bonded with the first abrasive layer 6, the lower surface of the first substrate layer 4 is bonded with the second abrasive layer 7 by the binder, and the second abrasive layer 7 is bonded away from the first substrate layer 4 by bonding. The binder is bonded with a second ba...
PUM
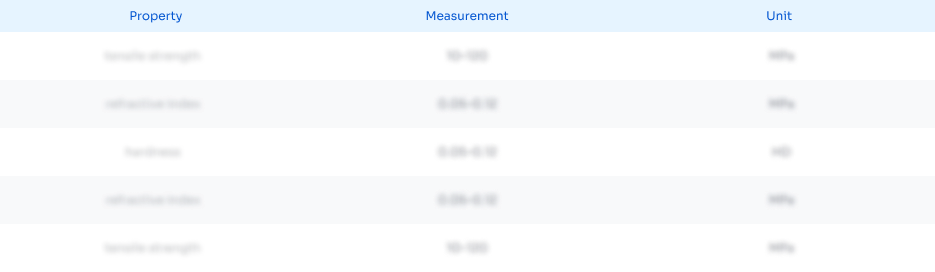
Abstract
Description
Claims
Application Information

- Generate Ideas
- Intellectual Property
- Life Sciences
- Materials
- Tech Scout
- Unparalleled Data Quality
- Higher Quality Content
- 60% Fewer Hallucinations
Browse by: Latest US Patents, China's latest patents, Technical Efficacy Thesaurus, Application Domain, Technology Topic, Popular Technical Reports.
© 2025 PatSnap. All rights reserved.Legal|Privacy policy|Modern Slavery Act Transparency Statement|Sitemap|About US| Contact US: help@patsnap.com