Stiffening component and method for manufacturing a stiffening component
A component and basic unit technology, which is applied in the field of strengthening components and for manufacturing strengthening components, and can solve the problems of difficult to manufacture crystalline morphological structures.
- Summary
- Abstract
- Description
- Claims
- Application Information
AI Technical Summary
Problems solved by technology
Method used
Image
Examples
Embodiment Construction
[0051] In the drawings, identical reference numerals denote identical or functionally identical components, unless otherwise stated. Directional terms such as "top", "bottom", "left", "right", "upper", "lower", "horizontal", "vertical", "front", "rear" and similar terms are used only These are for illustrative purposes and are not intended to limit the embodiments to the particular arrangements shown in the figures.
[0052] While specific embodiments have been illustrated and described herein, those skilled in the art will recognize that various alternative and / or equivalent implementations may be used in place of that illustrated and described without departing from the scope of the invention. specific example of . Generally, this application is intended to cover any adaptations or variations of the specific embodiments discussed herein.
[0053] Additive Manufacturing (ALM), Selective Laser Sintering (SLS) and Free Solid Fabrication (SFF) technologies, commonly referred t...
PUM
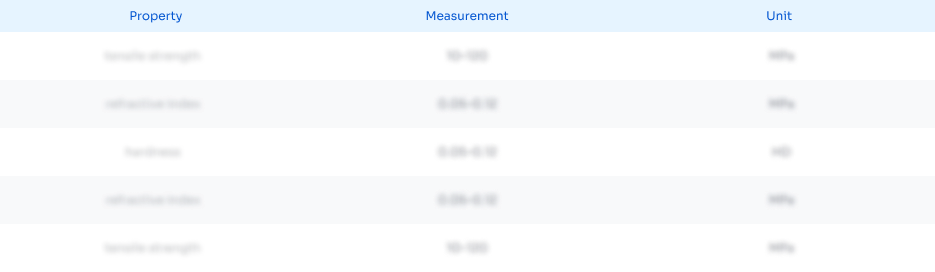
Abstract
Description
Claims
Application Information

- R&D
- Intellectual Property
- Life Sciences
- Materials
- Tech Scout
- Unparalleled Data Quality
- Higher Quality Content
- 60% Fewer Hallucinations
Browse by: Latest US Patents, China's latest patents, Technical Efficacy Thesaurus, Application Domain, Technology Topic, Popular Technical Reports.
© 2025 PatSnap. All rights reserved.Legal|Privacy policy|Modern Slavery Act Transparency Statement|Sitemap|About US| Contact US: help@patsnap.com