Preparing method and application of catalyst
A catalyst and additive technology, applied in chemical instruments and methods, physical/chemical process catalysts, chemical/physical processes, etc., can solve problems such as blanks, achieve unique components, simple production process, prolong thermal stability and service life Effect
- Summary
- Abstract
- Description
- Claims
- Application Information
AI Technical Summary
Problems solved by technology
Method used
Examples
Embodiment approach 1
[0023] Embodiment 1: A preparation method of a catalyst, the raw materials of the following parts by weight are prepared according to the following steps:
[0024] 50 parts of light rare earth raw ore powder including lanthanum and cerium
[0025] Including 30 parts of heavy rare earth raw ore powder of yttrium
[0026] Microsilica fume 32 parts
[0027] Zirconia 17 parts
[0028] Borax 20 parts
[0030] Titanium carbide 0.2 part
[0031] Tantalum carbide 0.4 parts
[0032] Additive 1 part
[0033] Described additive is boric acid;
[0034] Preparation steps:
[0035] 1) Dry ball milling the additive for 2 hours;
[0036] 2) Put the ball-milled additives together with other materials into a double-cone mixer and mix them thoroughly, and the mixing time is 20 hours;
[0037] 3) Pass through a 200-mesh sieve, pack, and serve.
Embodiment approach 2
[0038] Embodiment 2: a method for preparing a catalyst, the raw materials in the following parts by weight are prepared according to the following steps:
[0039] 60 parts of light rare earth raw ore powder including lanthanum and cerium
[0040] Including 40 parts of heavy rare earth raw ore powder of yttrium
[0041] Microsilica fume 38 parts
[0042] Zirconia 19 parts
[0043] Borax 24 parts
[0045] Titanium carbide 0.3 parts
[0046] Tantalum carbide 1.5 parts
[0047] The additive is calcium fluoride;
[0048] Preparation steps:
[0049] 1) Dry ball milling the additive for 10 hours;
[0050] 2) Put the ball-milled additives together with other materials into a double-cone mixer and mix them thoroughly, and the mixing time is 40 hours;
[0051] 3) Pass through a 200-mesh sieve, pack, and serve.
Embodiment approach 3
[0052] Embodiment 3: a method for preparing a catalyst, the raw materials in the following parts by weight are prepared according to the following steps:
[0053] 55 parts of light rare earth raw ore powder including lanthanum and cerium
[0054] Including 35 parts of heavy rare earth raw ore powder of yttrium
[0055] Microsilica fume 35 parts
[0056] Zirconia 18 parts
[0057] 22 parts of borax
[0058] Boron nitride 2 parts
[0059] Titanium carbide 0.25 parts
[0060] Tantalum carbide 0.45 parts
[0061] Additive 1.3 parts
[0062] The additives are half of strontium fluoride and half of aluminum fluoride;
[0063] Preparation steps:
[0064] 1) Dry ball milling the additive for 6 hours;
[0065] 2) Put the ball-milled additives together with other materials into a double-cone mixer and mix them thoroughly, and the mixing time is 30 hours;
[0066] 3) Pass through a 200-mesh sieve, pack, and serve.
PUM
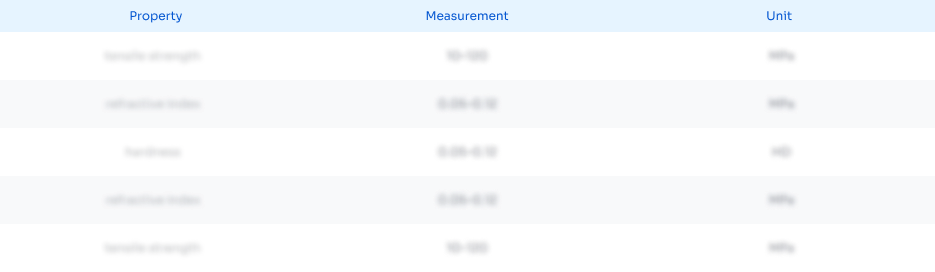
Abstract
Description
Claims
Application Information

- R&D Engineer
- R&D Manager
- IP Professional
- Industry Leading Data Capabilities
- Powerful AI technology
- Patent DNA Extraction
Browse by: Latest US Patents, China's latest patents, Technical Efficacy Thesaurus, Application Domain, Technology Topic, Popular Technical Reports.
© 2024 PatSnap. All rights reserved.Legal|Privacy policy|Modern Slavery Act Transparency Statement|Sitemap|About US| Contact US: help@patsnap.com