A wire rod rolling method for eliminating fine grains on the surface of low carbon steel
A technology of fine-grained, low-carbon steel, applied in the field of wire rod rolling to eliminate fine-grained surface of low-carbon steel, can solve unfavorable drawing or cold heading, cannot guarantee uniformity of structure, adverse effects on drawing performance, etc. To avoid the sharp drop of surface temperature, it is conducive to the uniformity of the temperature of the wire rod, and it is conducive to the rapid recovery of the temperature.
- Summary
- Abstract
- Description
- Claims
- Application Information
AI Technical Summary
Problems solved by technology
Method used
Image
Examples
Embodiment 1
[0019] The weight percentage components of the low-carbon steel in this example are shown in Table 1. The temperature in the heating section of the low-carbon steel slab is 950°C, the soaking section reaches 1050°C, the soaking time is 25min, and the rolling start temperature is 958°C , the finish rolling temperature inlet is 945°C, the water tank adopts 1 set of forward air-cooled nozzles, 9 sets of water-cooled nozzles and 3 sets of reverse air-cooled nozzles according to the rolling direction, the distance between the reverse nozzles is 0.5m, and the water pressure of the water-cooled nozzles before and after finishing rolling is 0.50 MPa, air cooling nozzle pressure 0.30MPa, 1# water tank flow rate 1200 / min, valve opening 26% before finishing rolling, 2# water tank flow rate 1150l / min, valve opening 25%; 1# water tank flow rate 785l / min after finishing rolling , valve opening 24%, 3# water tank flow 683l / min, valve opening 19%; 5# water tank 512l / min, valve opening 13%, 2# ...
Embodiment 2
[0021] The weight percentage components of the low-carbon steel in this example are shown in Table 1. The temperature in the heating section of the low-carbon steel slab is 945°C, the soaking section reaches 1060°C, the soaking time is 27min, and the rolling start temperature is 945°C , the finish rolling temperature inlet is 942℃, the water tank adopts 1 set of forward air-cooled nozzles, 9 sets of water-cooled nozzles and 3 sets of reverse air-cooled nozzles according to the rolling direction, the distance between the reverse nozzles is 0.5m, and the water pressure of the water-cooled nozzles before and after finishing rolling is 0.50 MPa, air-cooled nozzle pressure 0.30MPa, 1# water tank flow rate 1170l / min, valve opening 26% before finishing rolling, 2# water tank flow rate 1080l / min, valve opening 25%; 1# water tank flow rate 7921 / min after finishing rolling , valve opening 25%, 3# water tank flow 696l / min, valve opening 20%; 5# water tank 530l / min, valve opening 13%, 2# a...
PUM
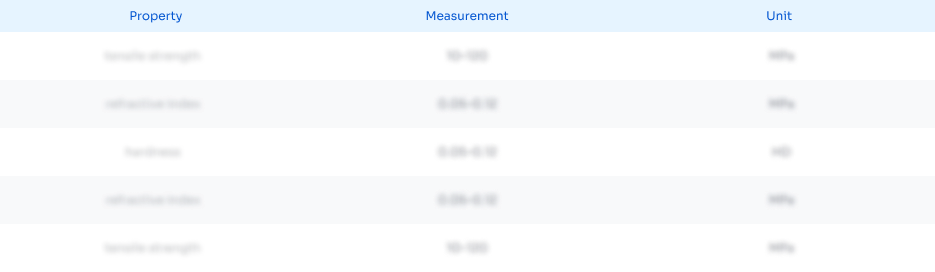
Abstract
Description
Claims
Application Information

- R&D
- Intellectual Property
- Life Sciences
- Materials
- Tech Scout
- Unparalleled Data Quality
- Higher Quality Content
- 60% Fewer Hallucinations
Browse by: Latest US Patents, China's latest patents, Technical Efficacy Thesaurus, Application Domain, Technology Topic, Popular Technical Reports.
© 2025 PatSnap. All rights reserved.Legal|Privacy policy|Modern Slavery Act Transparency Statement|Sitemap|About US| Contact US: help@patsnap.com