Automatic unstacking and bag removing production line and automatic unstacking and bag removing production method
A production method and production line technology, applied in the direction of destacking, packaging, transportation and packaging of objects, which can solve problems such as environmental pollution, adverse human health, and high labor intensity.
- Summary
- Abstract
- Description
- Claims
- Application Information
AI Technical Summary
Problems solved by technology
Method used
Image
Examples
Embodiment Construction
[0060] Examples such as figure 1 , figure 2 As shown, an automatic unstacking and bag unpacking production line includes a stacking conveyor 1 for stacking and conveying. One side of the 2 is provided with a bag receiving conveyor 3 for removing a single package from the stack, the output end of the bag receiving conveyor 3 is provided with a feeding belt conveyor 4, and the source end of the feeding belt conveyor 4 is provided with a The pre-pressing device 5 for pre-crushing the bulk materials in the sub-package, the output end of the pre-pressing device 5 is provided with a cutting device 10 for unpacking, and the block crushing device 11 for finely crushing the materials is provided under the cutting device 10. The output end of the material crushing device 11 is provided with a screening device 6 for separating the material from the packaging bag. Below the screening device 6 is provided a screw conveying device 7 for conveying the material. There is a waste bag colle...
PUM
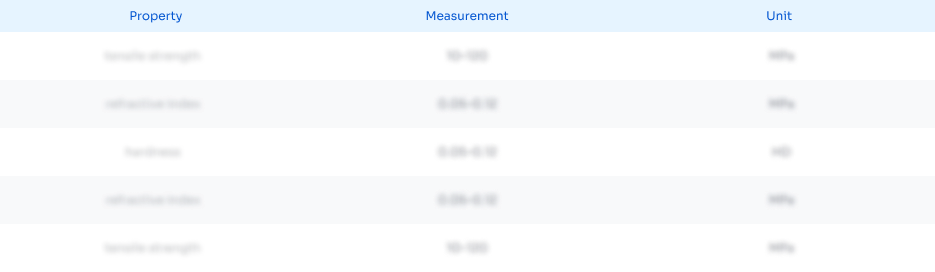
Abstract
Description
Claims
Application Information

- R&D Engineer
- R&D Manager
- IP Professional
- Industry Leading Data Capabilities
- Powerful AI technology
- Patent DNA Extraction
Browse by: Latest US Patents, China's latest patents, Technical Efficacy Thesaurus, Application Domain, Technology Topic, Popular Technical Reports.
© 2024 PatSnap. All rights reserved.Legal|Privacy policy|Modern Slavery Act Transparency Statement|Sitemap|About US| Contact US: help@patsnap.com