Assisted processing technology after oxidation bluing
An auxiliary processing and process technology, applied in the direction of metal material coating process, etc., can solve the problems of poor processing effect and complicated processing technology, and achieve the effect of simple processing method, beautiful oxide film and long service life
- Summary
- Abstract
- Description
- Claims
- Application Information
AI Technical Summary
Problems solved by technology
Method used
Examples
Embodiment Construction
[0009] The technical solution disclosed by the present invention is an auxiliary processing technology after oxidation bluing, which is characterized in that it includes the following steps: (1) After the workpiece is taken out from the bluing solution, it should be immediately rinsed in warm water, then rinsed in cold water, and finally boiled cleaning.
[0010] (2) Saponification: use civil soap 5%+95% water (H 2 O) Saponification, temperature 80-l00 ℃, time 3-l0min. Saponification is to form a thin film of iron stearate on the surface of the workpiece, fill the pores of the oxide film, and further improve the corrosion resistance and quality of the oxide film.
[0011] (3) After saponification, it must be washed with warm water (water temperature 60-80°C), remove the saponification liquid, and make it dry immediately.
[0012] (4) Oiling: After the workpiece is thoroughly dried, put 10# engine oil, transformer oil, and vaseline oil at a temperature of 80-90°C, the ratio i...
PUM
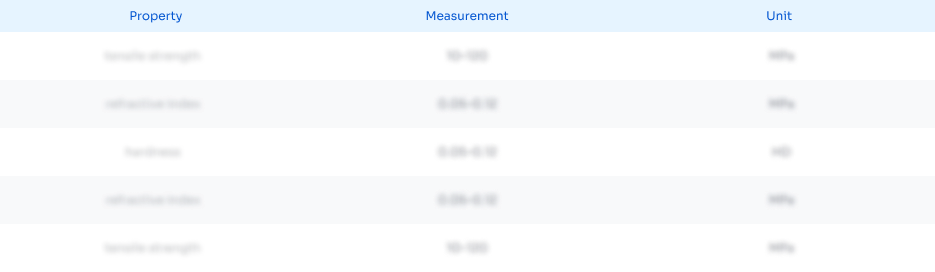
Abstract
Description
Claims
Application Information

- R&D
- Intellectual Property
- Life Sciences
- Materials
- Tech Scout
- Unparalleled Data Quality
- Higher Quality Content
- 60% Fewer Hallucinations
Browse by: Latest US Patents, China's latest patents, Technical Efficacy Thesaurus, Application Domain, Technology Topic, Popular Technical Reports.
© 2025 PatSnap. All rights reserved.Legal|Privacy policy|Modern Slavery Act Transparency Statement|Sitemap|About US| Contact US: help@patsnap.com