Method for compounding diaphragm and pole piece of wound laminated battery
A winding and diaphragm technology, which is applied in the direction of secondary batteries, battery pack parts, circuits, etc., can solve the problems of uneven coating of glue, excessive glue, closed cells, etc., and achieve firm adhesion and improved The effect of adhesion properties
- Summary
- Abstract
- Description
- Claims
- Application Information
AI Technical Summary
Problems solved by technology
Method used
Image
Examples
Embodiment 1
[0030] In a 5L blender, add 3L of N-methylpyrrolidone NMP, then add 100g of epoxy resin to dissolve, stir until a clear and transparent solution is formed, and place the dispersed epoxy resin solution in an open container , And then dipping the diaphragm substrate in the epoxy resin glue at a rate of 20HZ; such as figure 1 As shown, the polymerized monomer 2 adheres to the diaphragm substrate 1;
[0031] Add 100g of polyamide to another blender and dissolve it with NMP. After being evenly dispersed, pass the pole piece through the polyamide glue to complete the dip; figure 2 As shown, the cross-linking agent 3 adheres to the pole piece 6;
[0032] The dipped separator is brought into contact with the positive pole piece and a pressure of 0.2T is applied, and then the cross-linking curing reaction occurs through an oven at 80° C., that is, the composite of the separator and the positive pole piece is realized. Such as image 3 , 4 As shown, when the two are in contact and a certain...
Embodiment 2
[0033] Example 2: In a 5L blender, add 3L of deionized water, then add 100g of acrylic resin to dissolve, stir until a clear and transparent solution is formed, put the dispersed acrylic solution in an open container, and then place the diaphragm base with Dip in the glue of acrylic resin at a certain rate; add 100g of amino resin to another blender and dissolve it with deionized water. After uniformly dispersed, the diaphragm substrate is then immersed in amino resin at a certain rate. In the glue solution, the dipping is completed, and then the dipped separator is brought into contact with the negative pole piece and a pressure of 0.5T is applied, and then the cross-linking curing reaction occurs through an oven at 100°C, that is, the separator and the negative pole piece are realized Compound.
Embodiment 3
[0034] Example 3: In a 5L blender, add 3L of N-methylpyrrolidone NMP, then add 100g of hydroxyacrylic acid to dissolve it, stir until a clear and transparent solution is formed, place the dispersed hydroxyacrylic acid solution in an open container, and then The separator with the inorganic coating is dipped in the hydroxy acrylic glue at a certain rate; 100g of polyurethane is added to another blender and dissolved with NMP. After the dispersion is uniform, the inorganic coating The layer diaphragm passes through the polyurethane glue at a certain rate to complete the dipping, and then the dipped coated diaphragm is brought into contact with the positive pole piece and applied with a pressure of 0.1T, and then passed through an oven at 50°C and kept for more than 10 minutes The cross-linking and curing reaction takes place, that is, the composite of the coated separator and the positive pole piece is realized.
PUM
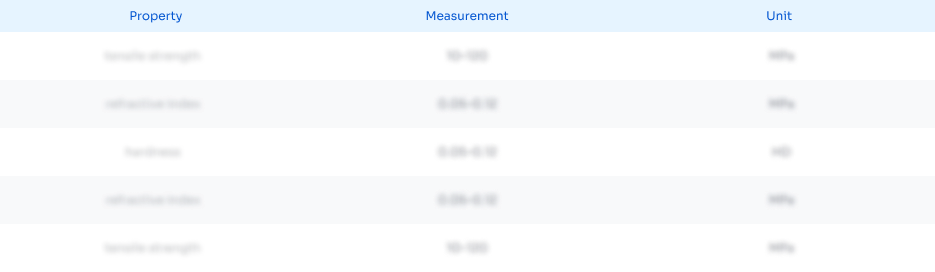
Abstract
Description
Claims
Application Information

- Generate Ideas
- Intellectual Property
- Life Sciences
- Materials
- Tech Scout
- Unparalleled Data Quality
- Higher Quality Content
- 60% Fewer Hallucinations
Browse by: Latest US Patents, China's latest patents, Technical Efficacy Thesaurus, Application Domain, Technology Topic, Popular Technical Reports.
© 2025 PatSnap. All rights reserved.Legal|Privacy policy|Modern Slavery Act Transparency Statement|Sitemap|About US| Contact US: help@patsnap.com