High-density knitted fabric, and production method and application thereof
A technology for knitted fabrics and production methods, which is applied in knitting, weft knitting, textiles, and papermaking, and can solve the problems of unimproved density and crispness, complicated processing methods, and insufficient elasticity of fabrics, so as to achieve delicate hand feeling and high production efficiency The effect of simple process and tight hand feeling
- Summary
- Abstract
- Description
- Claims
- Application Information
AI Technical Summary
Problems solved by technology
Method used
Image
Examples
Embodiment 1
[0035] On the 28G single-sided circular knitting machine, 82dtex-24f-polyester-nylon composite yarn (6+1 type, polyester as flap, nylon as core, nylon content 30%, nylon component crystallization temperature 75°C, melting point 195°C, fiber opening Nylon monofilament fineness is 1.0dtex, polyester monofilament fineness is 0.4dtex), plain weave weaving is carried out to obtain knitted gray fabric, and then 0.825% caustic soda is used in liquid flow dyeing machine to reduce the fiber opening at 120°C for 30 minutes , with a reduction rate of 10%, then dyeing at 132 degrees, and finally resin finishing and setting at 160 degrees to obtain a knitted fabric with a grammage of 180g / ㎡.
[0036] According to the KES method, the obtained knitted fabric has a lateral bending stiffness B value of 0.06gf.cm2 / cm, a longitudinal bending stiffness B value of 0.06gf.cm2 / cm, and a ventilation volume of 58cm according to the JISL1096-2010 method. 3 / cm 2 / sec.
Embodiment 2
[0038] On the 28G double-sided circular knitting machine, 82dtex-24f-polyester-nylon composite yarn (6+1 type, polyester as flap, nylon as core, nylon content 30%, nylon component crystallization temperature 75°C, melting point 195°C, fiber opening Afterwards, the nylon monofilament fineness is 1.0dtex, and the polyester monofilament fineness is 0.4dtex), and the knitted fabric is obtained by weaving cotton and wool tissue, and then using 0.7% caustic soda in the liquid flow dyeing machine to reduce the fiber opening at 125°C for 25 minutes , with a reduction rate of 14%, then dyeing at 135 degrees, and finally resin finishing and setting at 160 degrees to obtain a knitted fabric with a grammage of 300g / ㎡.
[0039] According to the KES method, the obtained knitted fabric has a transverse bending stiffness B value of 0.17gf.cm2 / cm and a longitudinal bending stiffness B value of 0.22gf.cm2 / cm; according to the JISL1096-2010 method, its ventilation volume is 23cm 3 / cm 2 / sec. ...
Embodiment 3
[0041] On the 28G double-sided circular knitting machine, 82dtex-24f-polyester-nylon composite yarn (6+1 type, polyester as flap, nylon as core, nylon content 20%, nylon component crystallization temperature 70°C, melting point 190°C, fiber opening Nylon monofilament fineness is 0.6dtex, polyester monofilament fineness is 0.4dtex) and 20D spandex are woven with Roman weave to obtain knitted gray fabric. The caustic soda was opened at 120°C for 30 minutes with a reduction rate of 15%, then dyed at 130°C, and finally resin-finished and set at 160°C to obtain a knitted fabric with a grammage of 300g / ㎡.
[0042]According to the KES method, the obtained knitted fabric has a transverse bending stiffness B value of 0.24gf.cm2 / cm and a longitudinal bending stiffness B value of 0.29gf.cm2 / cm; according to the JISL1096-2010 method, its ventilation volume is 28cm 3 / cm 2 / sec.
PUM
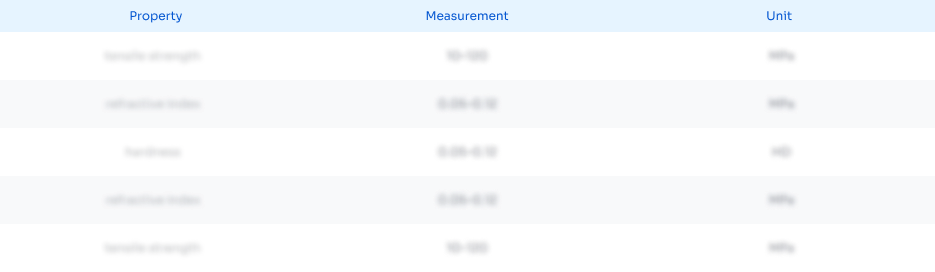
Abstract
Description
Claims
Application Information

- R&D Engineer
- R&D Manager
- IP Professional
- Industry Leading Data Capabilities
- Powerful AI technology
- Patent DNA Extraction
Browse by: Latest US Patents, China's latest patents, Technical Efficacy Thesaurus, Application Domain, Technology Topic, Popular Technical Reports.
© 2024 PatSnap. All rights reserved.Legal|Privacy policy|Modern Slavery Act Transparency Statement|Sitemap|About US| Contact US: help@patsnap.com