Hot galvanizing process
A hot-dip galvanizing and process technology, applied in the direction of hot-dip galvanizing process, metal material coating process, coating, etc., can solve the problems of incomplete metal surface treatment, reduce the amount of zinc dross in the zinc pot, and accelerate the precipitation of zinc dross, etc. Achieve good appearance, improve the appearance of the coating, and achieve high bonding strength
- Summary
- Abstract
- Description
- Claims
- Application Information
AI Technical Summary
Problems solved by technology
Method used
Examples
Embodiment 1
[0033] A hot-dip galvanizing process, comprising the steps of:
[0034] (1) degreasing water washing
[0035] Putting the workpiece into the degreasing solution for dipping and degreasing, the temperature of the degreasing is 40°C, and the time of the dipping and degreasing is 10 minutes;
[0036] (2) pickling
[0037] Put the degreased workpiece into a solution of 15% sulfuric acid and 0.1% thiourea for pickling, and the pickling temperature is 40°C;
[0038] (3) Ultrasonic cleaning
[0039] Clean the workpiece after pickling with ultrasonic wave to remove the oil and residual acid in the dead corner of the workpiece. Rinse in clean water;
[0040] (4) Preheating
[0041] Put the workpiece into the annealing furnace, remove the moisture on the surface of the workpiece, and preheat the workpiece to 130°C;
[0042] (5) heating
[0043] in H 2 and N 2 Under the protection of the workpiece, heat the workpiece to 710°C and keep the temperature for 30s to activate the surf...
Embodiment 2
[0053] A hot-dip galvanizing process, comprising the steps of:
[0054] (1) degreasing water washing
[0055] Put the workpiece into the degreasing solution for immersion degreasing, the temperature of the degreasing is 45°C, and the time of the immersion degreasing is 15min;
[0056] (2) pickling
[0057] Put the degreased workpiece into a solution of 17.5% sulfuric acid and 0.12% thiourea for pickling, and the pickling temperature is 50°C;
[0058] (3) Ultrasonic cleaning
[0059] Clean the workpiece after pickling with ultrasonic waves to remove oil stains and residual acid in dead corners of the workpiece. The content of trichlorethylene is 7.5%, the cleaning temperature is 55°C, the cleaning frequency is 50KHz, and the cleaning time is 2.5min. Rinse in clean water;
[0060] (4) Preheating
[0061] Put the workpiece into the annealing furnace, remove the moisture on the surface of the workpiece, and preheat the workpiece to 150°C;
[0062] (5) heating
[0063] in H 2...
Embodiment 3
[0073] A hot-dip galvanizing process, comprising the steps of:
[0074] (1) degreasing water washing
[0075] Putting the workpiece into the degreasing solution for dipping and degreasing, the temperature of the degreasing is 50°C, and the time of the dipping and degreasing is 20 minutes;
[0076] (2) pickling
[0077] Put the degreased workpiece into a solution of 20% sulfuric acid and 0.14% thiourea for pickling, and the pickling temperature is 60°C;
[0078] (3) Ultrasonic cleaning
[0079] Clean the workpiece after pickling with ultrasonic waves to remove oil and residual acid in the dead corners of the workpiece. The content of trichlorethylene is 10%, the cleaning temperature is 60°C, the cleaning frequency is 60KHz, and the cleaning time is 3min, and the workpiece is placed in the Rinse in clean water;
[0080] (4) Preheating
[0081] Put the workpiece into the annealing furnace, remove the moisture on the surface of the workpiece, and preheat the workpiece to 170°...
PUM
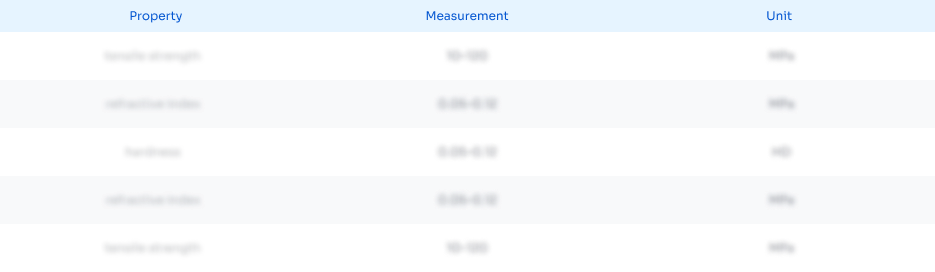
Abstract
Description
Claims
Application Information

- R&D
- Intellectual Property
- Life Sciences
- Materials
- Tech Scout
- Unparalleled Data Quality
- Higher Quality Content
- 60% Fewer Hallucinations
Browse by: Latest US Patents, China's latest patents, Technical Efficacy Thesaurus, Application Domain, Technology Topic, Popular Technical Reports.
© 2025 PatSnap. All rights reserved.Legal|Privacy policy|Modern Slavery Act Transparency Statement|Sitemap|About US| Contact US: help@patsnap.com