Hot top casting process for phi 784-mm 7xxx-series superhard aluminum alloy round bar
A technology of hard aluminum alloy and hot top casting, which is applied in the field of metal material forming, can solve the problems such as loose pores of bright grains, and achieve the effect of reducing the internal stress of casting
- Summary
- Abstract
- Description
- Claims
- Application Information
AI Technical Summary
Problems solved by technology
Method used
Image
Examples
Embodiment 1
[0039] The hot-top casting process of the 7xxx series superhard aluminum alloy round rod, the aluminum alloy round rod contains the following chemical components by mass: Si0.25%; Fe0.4%; Cu1.6%; Mn0.25%; Mg2.6%; Cr0.2%; Zn5.6%; Ti0.15%; Zr0.03%;
[0040] Its preparation process comprises the following steps:
[0041] a. Material preparation: select low-iron and low-silicon aluminum ingots, aluminum-manganese alloys, aluminum-copper master alloy ingots, aluminum-lead master alloy ingots and magnesium ingots according to the ratio;
[0042] b. Smelting: Add other raw materials except magnesium ingots to the furnace for smelting, the melting temperature is 760°C, and add magnesium ingots after complete melting, refining and slag removal;
[0043] c. Stirring: the electromagnetic stirrer is used to stir to ensure that the raw materials in the furnace can be melted quickly and the temperature is uniform;
[0044] d. Refining: the refining process includes smelting furnace refin...
Embodiment 2
[0057] The hot-top casting process of the 7xxx series superhard aluminum alloy round rod, the aluminum alloy round rod contains the following chemical components by mass: Si0.25%; Fe0.4%; Cu1.55%; Mn0.25%; Mg2.55%; Cr0.19%; Zn5.6%; Ti0.15%; Zr0.03%;
[0058] Its preparation process comprises the following steps:
[0059] a. Material preparation: select low-iron and low-silicon aluminum ingots, aluminum-manganese alloys, aluminum-copper master alloy ingots, aluminum-lead master alloy ingots and magnesium ingots according to the ratio;
[0060] b. Smelting: Add other raw materials except magnesium ingots to the furnace for smelting, the melting temperature is 755°C, and add magnesium ingots after complete melting, refining and slag removal;
[0061] c. Stirring: the electromagnetic stirrer is used to stir to ensure that the raw materials in the furnace can be melted quickly and the temperature is uniform;
[0062] d. Refining: the refining process includes smelting furnace r...
PUM
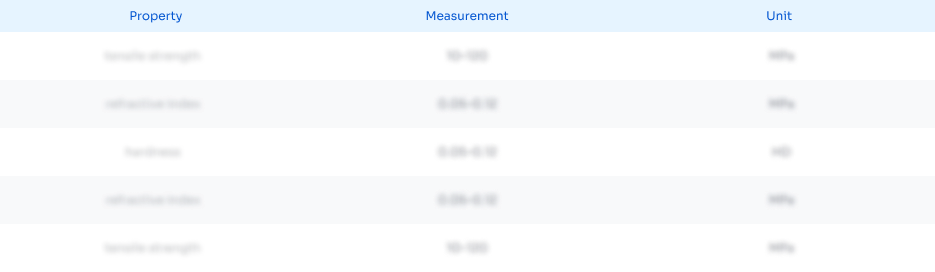
Abstract
Description
Claims
Application Information

- R&D Engineer
- R&D Manager
- IP Professional
- Industry Leading Data Capabilities
- Powerful AI technology
- Patent DNA Extraction
Browse by: Latest US Patents, China's latest patents, Technical Efficacy Thesaurus, Application Domain, Technology Topic, Popular Technical Reports.
© 2024 PatSnap. All rights reserved.Legal|Privacy policy|Modern Slavery Act Transparency Statement|Sitemap|About US| Contact US: help@patsnap.com