Robotized spiral drilling method and system for laminated structure of airframe
A technology of laminated structure and aircraft fuselage, which is applied in the direction of manufacturing tools, details of milling machine equipment, metal processing equipment, etc., can solve the problems of difficult to use, unfavorable terminal hole-making actuator attachment, low efficiency in processing laminated structure, etc. Achieve the effect of suppressing the exciting force, improving the hole-making efficiency, and reducing the tool wear
- Summary
- Abstract
- Description
- Claims
- Application Information
AI Technical Summary
Problems solved by technology
Method used
Image
Examples
Embodiment Construction
[0023] Such as figure 1 As shown, a method for robotized spiral hole making for aircraft fuselage stacked structure, which is applied to a robotized screw hole making system, includes the following steps:
[0024] (1) According to the diameter of the tool and the diameter of the hole to be made on the laminated structure of the fuselage, adjust the tool revolution radius e to the required setting value;
[0025] (2) Tool 8 to match the high rotation speed n of the top layer component material s1 , low revolution speed n ω1 and large feed pitch P 1 , performing spiral drilling on the top layer member 101;
[0026] (3) At the interface 103 of the stacked structure of the fuselage, the high rotation speed, low revolution speed, and large feed pitch of the tool are adjusted by n s1 , n ω1 ,P 1 tuned to match the n of the underlying component material s2 , n ω2 ,P 2 ;
[0027] (4) Tool to match the high rotation speed n of the underlying component material s2 , low revol...
PUM
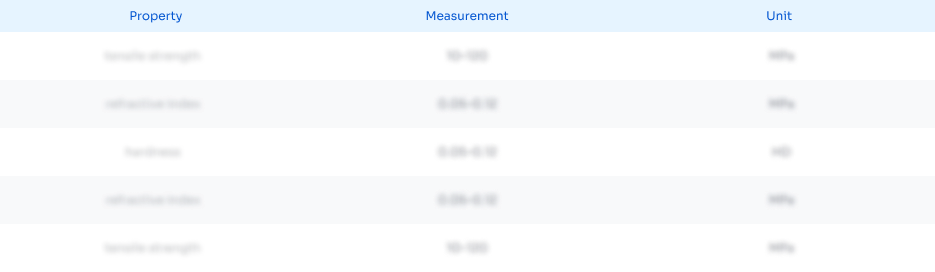
Abstract
Description
Claims
Application Information

- R&D Engineer
- R&D Manager
- IP Professional
- Industry Leading Data Capabilities
- Powerful AI technology
- Patent DNA Extraction
Browse by: Latest US Patents, China's latest patents, Technical Efficacy Thesaurus, Application Domain, Technology Topic, Popular Technical Reports.
© 2024 PatSnap. All rights reserved.Legal|Privacy policy|Modern Slavery Act Transparency Statement|Sitemap|About US| Contact US: help@patsnap.com