Treating method for vanadium slag roasting tail gas
A treatment method and tail gas technology, applied in the direction of gas treatment, separation methods, chemical instruments and methods, etc., can solve the problems of unutilized waste heat of tail gas, difficulty in achieving standard discharge, and difficult treatment of sulfide, so as to save steam consumption and save Coal consumption of the boiler and the effect of reducing the amount of spraying of circulating water
- Summary
- Abstract
- Description
- Claims
- Application Information
AI Technical Summary
Problems solved by technology
Method used
Image
Examples
Embodiment 1
[0149] From the tail of a vanadium pentoxide rotary kiln with an annual production capacity of 5,000 tons, the exhausted roasting tail gas at 350-450°C is connected to a multi-tube ceramic cyclone through the main flue of the rotary kiln. After cyclone dust removal, 90% The vanadate dust is collected in the collector at the lower part of the cyclone, and the exhaust gas is passed into the waste heat boiler.
[0150]Pass the desalted water to be heated into the deaerator, and exchange heat with the hot steam coming from the steam accumulator. After the temperature rises to 100-110°C, thermal deaeration is carried out. The desalinated water after oxygen removal is sent to the hot water heater of the waste heat boiler through the boiler feed water pump, and after heat exchange with the tail gas through the longitudinal fin heat pipe, the desalinated water becomes hot water at 150-160 °C. The tail gas then exchanges heat with the 150-160°C desalted water heated by the heater at th...
PUM
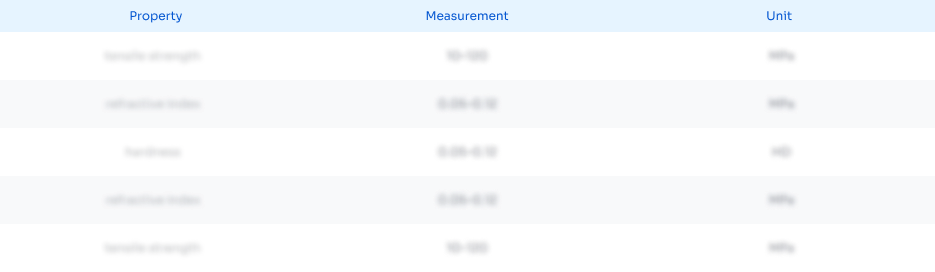
Abstract
Description
Claims
Application Information

- R&D
- Intellectual Property
- Life Sciences
- Materials
- Tech Scout
- Unparalleled Data Quality
- Higher Quality Content
- 60% Fewer Hallucinations
Browse by: Latest US Patents, China's latest patents, Technical Efficacy Thesaurus, Application Domain, Technology Topic, Popular Technical Reports.
© 2025 PatSnap. All rights reserved.Legal|Privacy policy|Modern Slavery Act Transparency Statement|Sitemap|About US| Contact US: help@patsnap.com